Die Herstellung von Faserbeton, insbesondere von Spritzbeton, kann bei Betonproduzenten manchmal zu Kopfschmerzen führen. Normalerweise wird Faserbeton nur für spezielle Projekte benötigt. In diesem Fall muss die Betonanlage entsprechend ausgestattet sein und zuverlässig arbeiten. Im Folgenden werden einige wichtige Punkte genannt, die dazu beitragen können, hochwertigen Faserbeton, insbesondere bei Verwendung als Spritzbeton, herzustellen.
.jpg)
Rohmaterialien und Mischrezepte für Faserbeton
Das Wichtigste bei der Herstellung von Faserbeton für die Verwendung als Spritzbeton ist, nur Materialien von hoher Qualität und konstanter Zusammensetzung zu verwenden.
Die maximale Korngröße der Zuschläge für Spritzbeton beträgt 8-10 mm, da sonst Probleme beim Spritzen programmiert werden, weil größere Körner die Düse verstopfen können.
Die benötigte Zementmenge ist ziemlich hoch, manchmal sogar 500 kg/m3. Es werden verschiedene andere Bindemittel eingesetzt, um einen Teil des Zements zu ersetzen, z. B. Mikrosilika oder Kalksteinmehl. Bei Faserbeton für die Verwendung als Spritzbeton liegt das W/B-Verhältnis normalerweise unter 0,45, was bedeutet, dass es ohne die Hilfe von Chemikalien fast unmöglich ist, eine für gute Verarbeitbarkeit ausreichende Konsistenz des Betons zu erzielen. Mit den richtigen Mengen an geeigneten Zusatzmitteln jedoch kann Faserbeton so hergestellt werden, dass er optimal zum Pumpen und Spritzen geeignet ist.
Fasern im Beton werden normalerweise als Bewehrung verwendet, um Risse im ausgehärteten Beton zu vermeiden oder die Feuerbeständigkeit zu erhöhen. Die am häufigsten verwendeten Typen sind Stahl-, Kunststoff- oder Glasfasern.
Beim Spritzen wird dem Beton in der Spritzmaschine ein Beschleuniger zugesetzt. Der Beschleuniger beeinflusst den Erstarrungs- und Aushärtungsprozess und verbessert damit die Fähigkeit des Betons, an Wänden und insbesondere Decken zu haften.
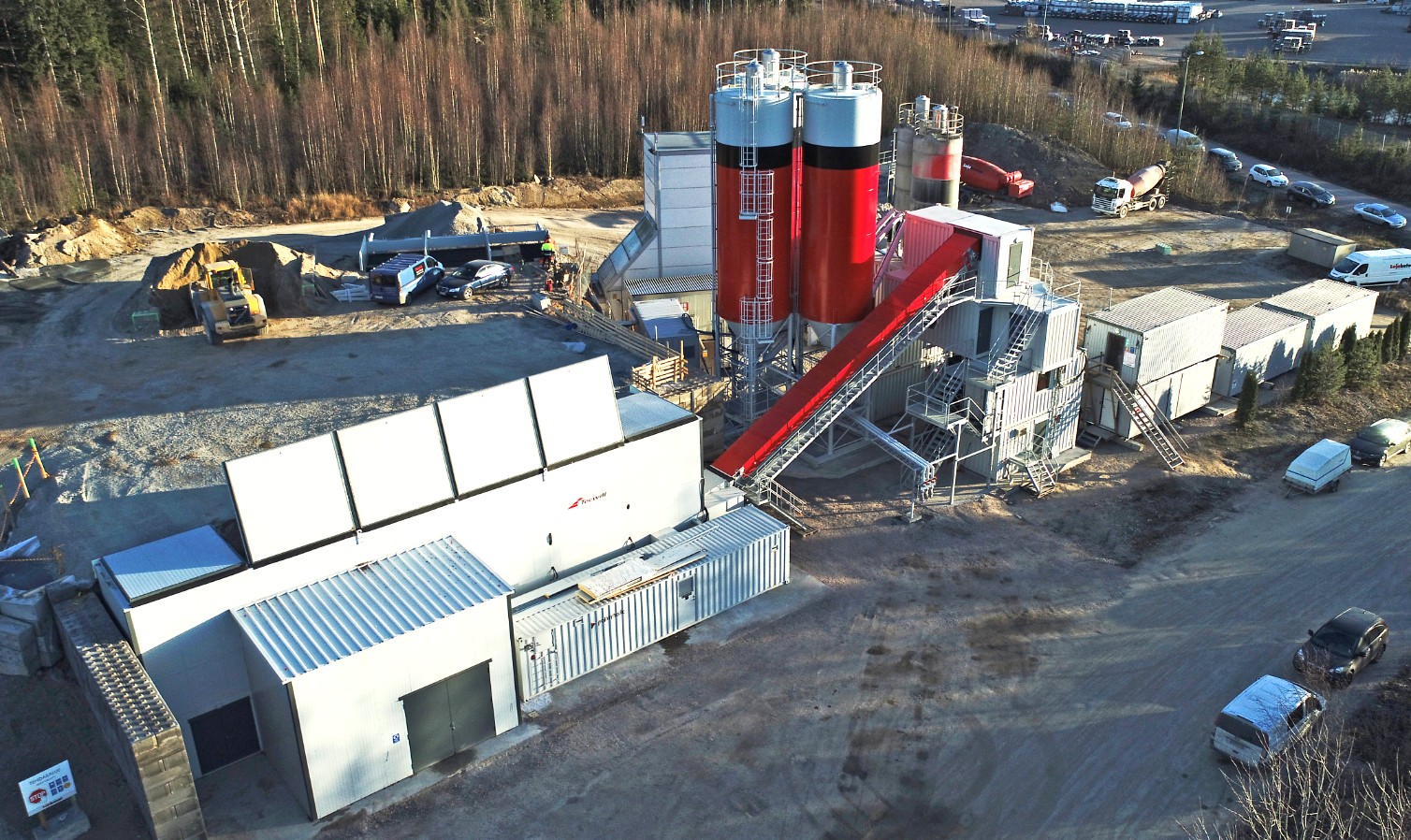
Anforderungen an das Betonwerk bei Herstellung von Faserbeton
Die Herstellung von hochwertigem Faserbeton stellt einige Anforderungen an das Betonwerk.
Zum einen sind im Fertigungsprozess genau arbeitende Dosiergeräte und Verwiegungssysteme unabdingbar, wobei die Standardabweichung von Charge zu Charge so gering wie möglich sein sollte. Wenn die Menge der Zuschläge stark schwankt, bedeutet das, dass sich jeweils auch die Menge der benötigten Bindemittel und der Wasserbedarf der Mischung verändern.
Der zweite relevante Punkt im Herstellungsprozess ist der Gesamtwassergehalt in der Mischung. Die Messung der Feuchtigkeit der Zuschläge und die Anpassung der Menge an Zugabewasser, das der Mischung zugesetzt werden soll, muss automatisch erfolgen. Insbesondere bei Mischungen mit einem niedrigen W/B-Verhältnis, wirkt sich bereits ein kleiner Fehler bei der Berechnung der Wassermenge, der durch einen falschen Wert der Zuschlagfeuchte verursacht wird, negativ aus. Eine ungenaue Dosierung und eine ineffektive Feuchtemessung werden in der Regel nur anhand von Labortests entdeckt, negative Einflüsse auf die Verarbeitbarkeit und Erstarrung machen sich jedoch bereits beim Betonieren bzw. Spritzen bemerkbar.
Weitere relevante Anforderungen an das Betonwerk sind eine hochentwickelte Anlagensteuerung und ein Hochleistungsmischer. Die Anlagensteuerung muss dafür sorgen können, dass alle Betoninhaltsstoffe genau dosiert werden, dass die Feuchtigkeit der Zuschlagstoffe genau gemessen wird und dass das W/B-Verhältnis sowie die Betonkonsistenz automatisch kontrolliert werden. Mischer, die perfekt zum Mischen von Faserbeton geeignet sind, sind z. B. Planeten-Gegenstrommischer oder Doppelwellenzwangsmischer.
.jpg)
Wie werden die Fasern dosiert und was sind die Vor- und Nachteile verschiedener Dosiermethoden?
1. Faserdosierung direkt in die Trommel des Fahrmischers
Nachdem der Beton in die Fahrmischertrommel abgeben wurde, fährt der LKW zur Faserdosierstation, wo die Fasern dem Beton entweder manuell oder über ein Dosierband hinzugefügt werden.
Vorteile
+ Das Mischen des Betons mit dem Mischer der Anlage erfordert weniger Zeit.
+ Keine Faserrückstände auf Fördereinrichtungen und damit auch nicht in Beton, der keine Fasern enthalten soll.
Nachteile
- Die Zugabe der Fasern und das Mischen dauern lange.- Trotz der längeren Mischzeit kann der Beton immer noch sehr inhomogen und die Fasern nicht gleichmäßig verteilt sein. Es können Verklumpungen von Fasern, sogenannte „Igel“ auftreten, die sich leicht in Schläuchen, Rohren oder Düsen festsetzen und zu Verstopfern führen können.
- Diese Dosierungsmethode ist nicht für Kunststofffasern geeignet.
2. Dosierung der Fasern direkt in den Mischer der Betonmischanlage
Bei Verwendung dieser Dosiermethode ist eine geeignete Dosierungsvorrichtung für den Mischer erforderlich.
Vorteile
+ Keine Faserrückstände auf Fördereinrichtungen und damit auch nicht in Beton, der keine Fasern enthalten soll.
Nachteile
- Platz für die Dosieranlage im Mischerbereich erforderlich.- Es können Verklumpungen von Fasern, sogenannte „Igel“ auftreten, die sich leicht in Schläuchen, Rohren oder Düsen festsetzen und zu Verstopfern führen können.
- Diese Dosiermethode erfordert eine längere Mischzeit, wodurch die Produktionsleistung der Betonmischanlage verringert wird.
3. Dosieren der Fasern auf das Wiegeband
In den meisten Betonwerken werden die Zuschlagstoffe auf einem Wiegeband verwogen. In diesem Fall kann die Faserdosieranlage möglicherweise im Bereich am Wiegeband installiert werden, sodass die Fasern auf die Zuschläge auf dem Wiegeband dosiert werden können.
Vorteile
+ Keine Faserrückstände auf Fördereinrichtungen und damit auch nicht in Beton, der keine Fasern enthalten soll.
Nachteile
- Platz für die Dosieranlage im Wiegebandbereich erforderlich.- Es können Verklumpungen von Fasern, sogenannte „Igel“ auftreten, die sich leicht in Schläuchen, Rohren oder Düsen festsetzen und zu Verstopfern führen können.
- Diese Dosiermethode erfordert eine längere Mischzeit, wodurch die Produktionsleistung der Betonmischanlage verringert wird.
4. Dosieren von Fasern auf die auf dem „fliegenden“ Wiegeband fließenden Zuschlagstoffe
Diese Methode kann nur bei der Verwendung des „fliegenden“ Zuschlagdosier- und -verwiegungssystem von Tecwill in Verbindung mit einer automatischen Faserdosieranlage, die neben der Zuschlagsiloeinheit installiert ist, angewendet werden.
Während die Zuschlagstoffe auf dem Wiegeband „fließen“, werden die Fasern kontinuierlich auf das dünne Zuschlagstoffbett dosiert. Dies führt zu einer sehr guten Vormischung von Fasern und Zuschlagstoffen, schon bevor diese in den Zuschlagzwischenbehälter gelangen. Mit dieser Methode wird eine Igelbildung vermieden und die Mischleistung der Anlage wird nicht beeinträchtigt.
Vorteile
+ Keine Igelbildung.+ Keine Faserrückstände auf Fördereinrichtungen und damit auch nicht in Beton, der keine Fasern enthalten soll.
+ Optimale Faserverteilung und homogener Beton trotz kurzer Mischzeit.
Nachteile
- Platz für die Dosieranlage im Bereich der Zuschlagsiloeinheit erforderlich.
.jpg)
Resümee
Für die Herstellung von Faserbeton, insbesondere wenn es um Spritzbeton geht, sind hochwertige Materialien und geeignete Mischrezepturen erforderlich. Genau arbeitende Dosiervorrichtungen, eine möglichst geringe Standardabweichung von Charge zu Charge, eine genaue Feuchtemessung der Zuschlagstoffe und ein guter Zwangsmischer sind unabdingbar. Eine ungeeignete Faserdosierung kann die Qualität des Betons beeinträchtigen und zu Problemen, insbesondere bei der Verarbeitung von Spritzbeton, führen.
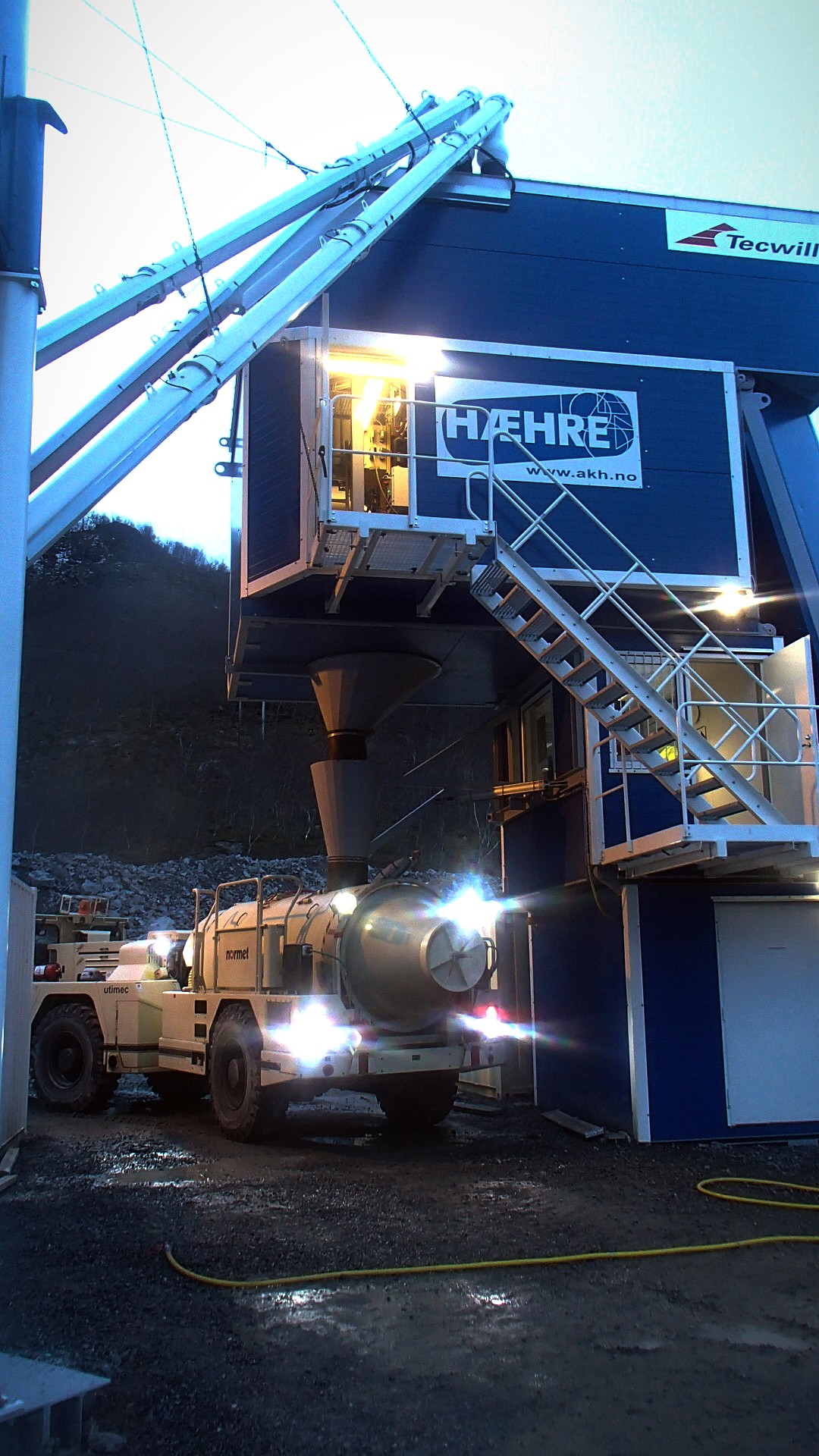
Tecwill Betonwerke und Faserbeton
Eine automatische Faserdosierung in Verbindung mit Tecwills „fliegendem“ Zuschlagdosier- und -verwiegungssystem ist die beste Lösung, wenn es darum geht, hochwertigen und konstant gleichmäßigen Faserbeton herzustellen, ohne die Produktionsleistung der Betonmischanlage zu beeinträchtigen.
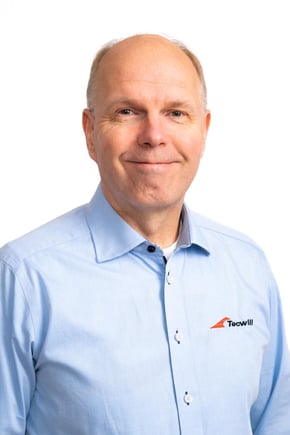