What distinguishes high-strength concrete from conventional mix designs, and why is it needed? This blog delves into the nuances of high-strength concrete production and the pivotal role of proper materials, precise temperature control and accurate dosing in ensuring its quality.
What is high-strength concrete, and why use it?
The difference between standard concrete and high-strength concrete, also known as high-performance concrete (HPC) or high-psi concrete, lies in their compressive strength. While standard concrete has a compressive strength of up to 50 MPa (7,000 psi), high-performance concrete has 50–120 MPa (7,000–17,000 psi), and ultra-high-performance concrete (UHPC) has over 120 MPa (17,000 psi). These values vary slightly from country to country.
High-strength concrete is typically used in frame structures of a large range of buildings. Skyscrapers, high-rise buildings and bridges often have impractically massive columns, beams and other structures if standard concrete is used. With high-strength concrete, it is possible to have more filigree, slender construction, which leads to more usable space inside buildings. It also gives these buildings a better appearance from the architectural point of view. And structures made of high-psi concrete have a higher longevity, strength and durability.
Another significant benefit of high-strength concrete is the cost savings from reduced raw material usage. A 25% reduction in concrete usage can translate into approximately 20% savings in raw materials. This reduction in material use is particularly crucial for cement, given its significant carbon footprint. By reducing cement usage, it is possible to achieve corresponding reductions in carbon dioxide emissions.
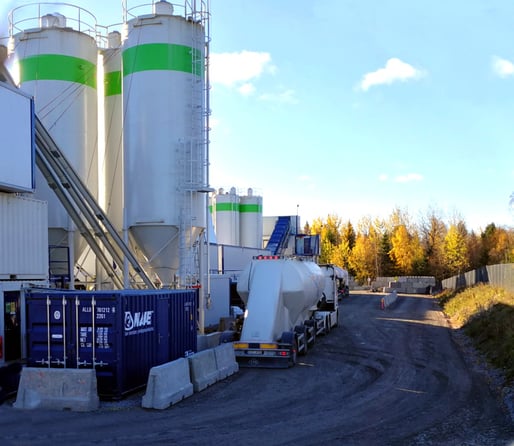
Plant requirements
There are two methods of producing concrete – by using either a wet batch or dry batch plant.
In dry concrete batching plants, components are only dosed, with the actual mixing occurring later in a truck mixer via free-fall mixing. For this reason, dry mix plants are generally not suitable for the production of HPC. The mixing result is not good enough, and the mixing time can extend to 15–20 minutes. This also increases the air content in the concrete mix, whereas the mixer drum wears out quickly.
The production of high-strength concrete is best done in a wet mix batch. The concrete is mixed with the compulsory mixer inside the plant. This ensures all materials are properly and reliably mixed and perfect concrete homogeneity is achieved.
Mixer choice
A concrete plant needs a good-quality concrete mixer to mix high-strength concrete. This should be either a planetary countercurrent mixer or a twin-shaft mixer. Planetary countercurrent mixers are typically the preferred choice, as they help avoid the unfavorable side effect of increased air content in the concrete.
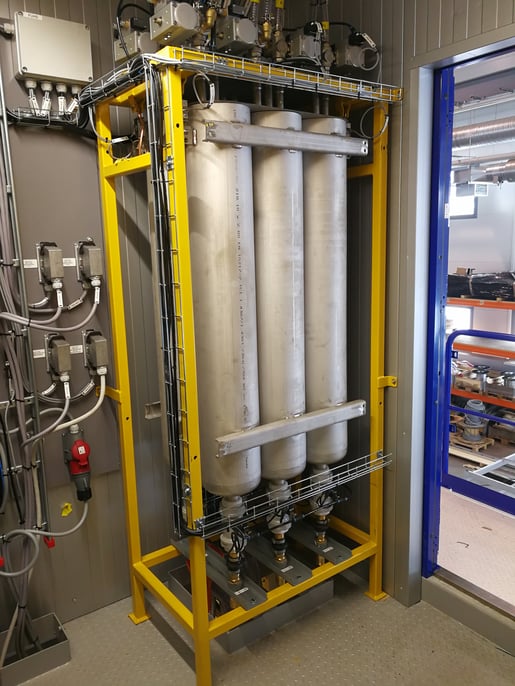
Materials used in high-strength concrete production
High-quality materials are an absolute must for high-strength concrete production. Admixtures, crushed gravel, coarse sand and different binders are all important ingredients.
HPC requires a lot of binder material, in some cases up to 650 kg/m3 (1,100 lb/yd3). Besides cement, the most common binders are fly ash, limestone powder, ground granulated blast-furnace slag (GGBFS) and micro silica. Fly ash, limestone powder and GGBFS replace some cement and enhance concrete workability, reduce water usage and prevent high concrete temperatures. Micro silica is used to achieve an even higher compressive strength.
The water-cement ratio of high-strength concrete is generally very low, usually between 0.2 and 0.3. The low water content in the mix leads to reduced workability. This is a challenge that can only be met with special concrete admixtures such as a superplasticizer admixture. Superplasticizers are added to concrete to enhance its mixing, workability and pumpability.
Accurate aggregate moisture measurement and dosing
Aggregate moisture significantly affects the amount of water in a mix. Therefore, it is very important to know the exact aggregate moisture content when producing HPC.
Automatic aggregate moisture measurement and calculation of water adjustments ensure seamless operations. Due to the low HPC water-cement ratio, even a small mistake in moisture measuring and calculations may ruin the whole batch.
Similarly important are accurate dosing devices and weighing systems. The deviation in dosing from batch to batch should be as small as possible. A significant variation in aggregate dosing between two batches leads to errors in the amount of aggregates dosed and the total water content of the concrete batch.
The importance of concrete temperature control
Maintaining the concrete temperature within a specified range is very important in HPC production, particularly for large-scale construction projects. This means the plant must be able to measure the temperature of all raw materials – including cement, water and especially aggregates.
In winter, variation in aggregate temperatures can be too high. To avoid this, the plant should be equipped with a proper aggregate and water heating system and a temperature control system. These will take care of aggregate heating in bins and sand piles. The control system also adjusts the concrete temperature according to the desired temperature value.
In warm weather, it may be necessary to cool down water, cement and aggregates to keep the concrete at the desired temperature. Sometimes, chilled water or even flaked ice can be added. While HPC hardens faster at higher temperatures, excessively high temperatures can lead to issues like cracks.
Additionally, measures must be taken to protect and properly cure the concrete produced, with careful supervision throughout the hardening process. By using retardants, it’s possible to slow down the hardening process and achieve a better concrete quality.
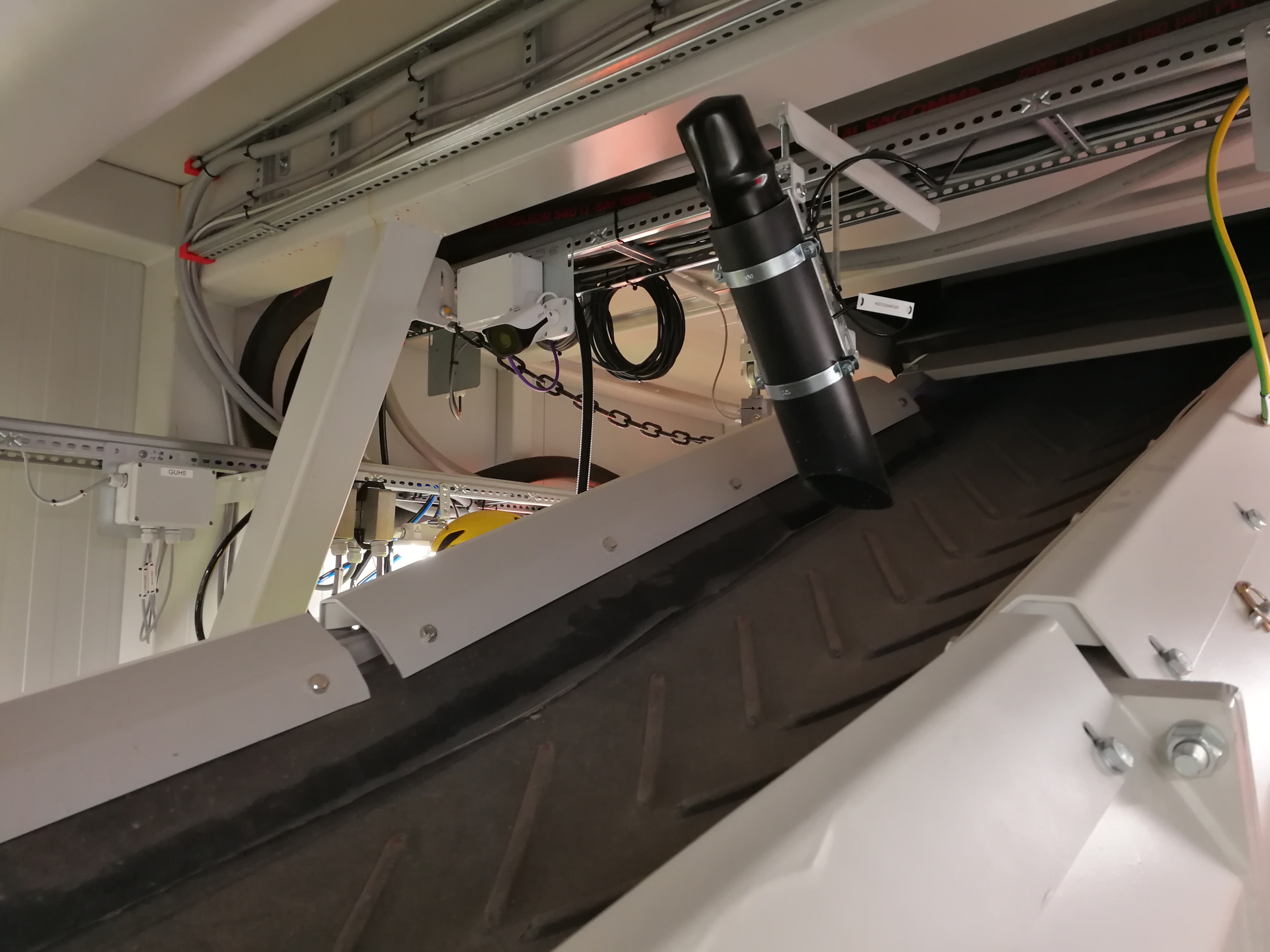
Summary
A good quality wet batch concrete plant with an efficient mixer makes producing high-strength concrete just as achievable as producing regular concrete.
A control system is another important factor. Such a system is critical to ensuring fully automatic temperature control, moisture measurement and correction and precise material dosing.
An accurate weighing system and improved aggregate moisture control are a must.
Tecwill plants for high-strength concrete production
All of Tecwill’s concrete plant models are appropriate for producing high-strength concrete.
Moreover, Tecwill’s solutions for aggregate moisture measuring, dosing as well as aggregate and water heating are extremely accurate and precise – just as the systems are for temperature and quality control. These solutions operate successfully under the most challenging conditions globally, guaranteeing reliable production of high-quality HPC.
If you want to receive further information, we are happy to answer all your questions.
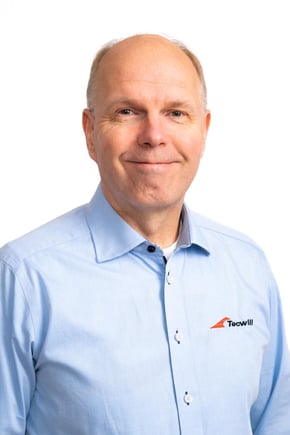