Precast elements and concrete products
The best concrete in the world for precast elements, paving stones and concrete blocks.
TABLE OF CONTENTS
Tecwill concrete plant for precast factory and concrete products
In a precast plant, each batch must be produced within the required dosing, moisture and temperature tolerances to ensure the highest quality product. Tecwill has developed the following unique features to guarantee homogeneous production:
- Improved aggregate moisture control leads to the right slump and water-to-cement ratio
- Automatic self-learning control of dosing deviation results in huge production savings, both in time and materials
- Precise batch concrete temperature
- The concrete batch plant is integrated within the precast factory, including concrete distribution, order points, aggregate and the water heating system
Modules of the Tecwill precast factory concrete plant
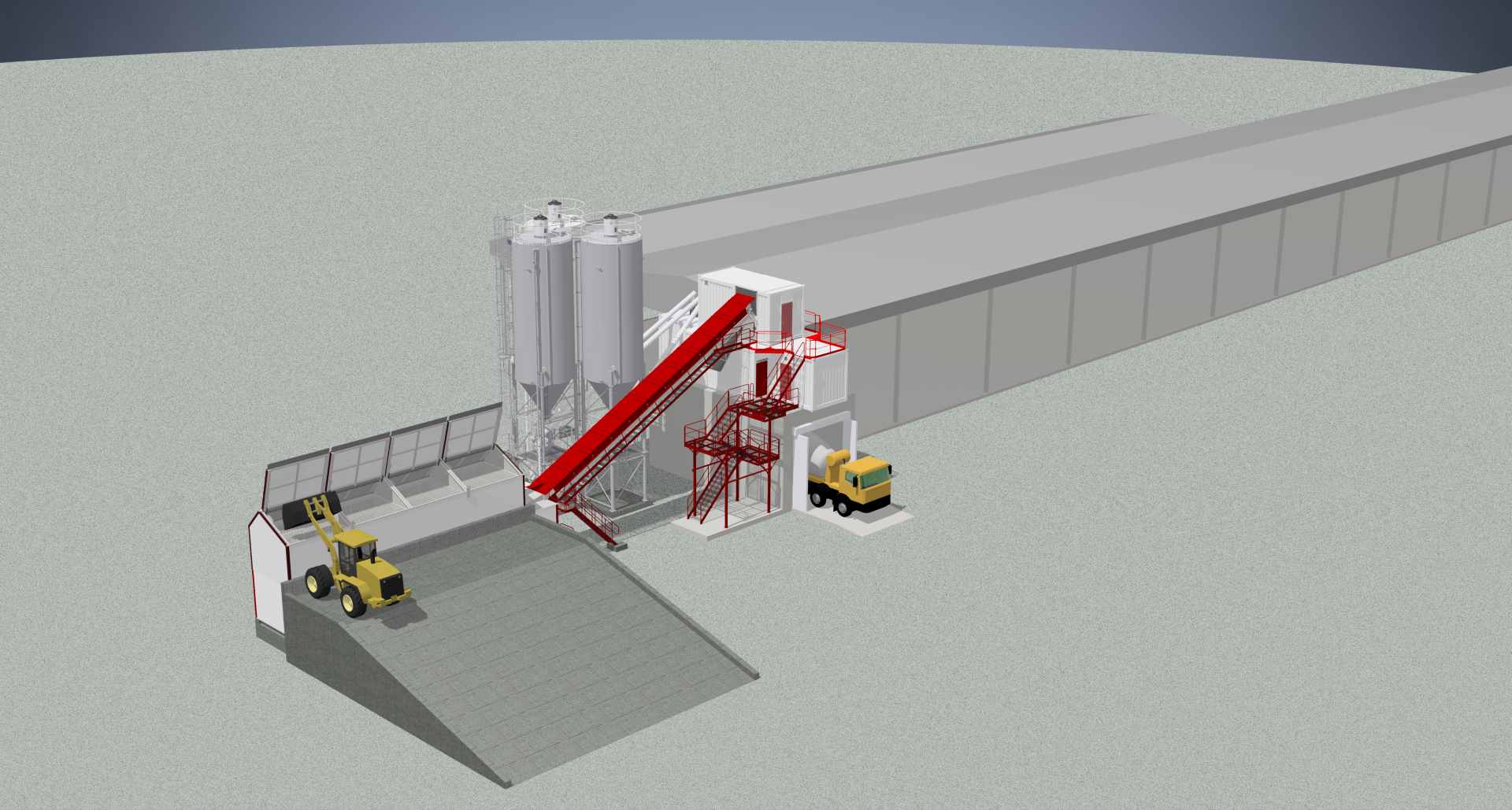
Delivery of a precast factory concrete plant
Our modular and high-performance precast plants are designed according to our customers’ needs and to suit their precast factory layout. Our precast concrete plant can be winterized while maintaining the tightest tolerances in the industry. All plants are pre-wired and tested before being shipped.
- First meeting
- Layout and technical solution
- Schedule, contract and budget
- Manufacturing
- Transport and installation
- Production start
- Production monitoring and optimization
Precast and concrete product factory concrete plant models
Our plants can produce all types of concrete for high-quality precast products, including:
- Wall panels, beams and pillars
- Steps, septic tanks and stormwater elements
- Piles and poles
- Hollow-core slabs with low slump concrete
- Elements with self-consolidating concrete
- Masonry elements, blocks and paving stones
- Colored concrete using powder, C pigment or granule pigments
The Arcamix concrete mixing plant, integrated within the production hall layout and equipped with a Tecwill “flying” weighing system and a planetary countercurrent mixer, is the solution for concrete production in a large precast factory.
Learn moreThe Cobra product line offers a concrete production solution with a small footprint for small and medium-sized block-paving stone and concrete product factories. The compact size allows a flexible layout.
Learn moreWith minor modifications and additions, our standard plant models can be easily customized to customer requirements for various applications.
Learn moreWhy choose Tecwill – how are we different?
Based on AI developed
in-house, Tecwill’s
dosing and weighing algorithm guarantees
high-quality precast concrete.
In a precast plant, each batch produced must be within the required dosing, moisture and temperature tolerances.
- Homogenous mixing
- Right temperature
- Correct slump for wet and dry mixes
Tecwill’s high-precision “flying” weighing system saves up to 30 kg/m3
(50 lb/yd3) in cement and reduces CO2 emissions in concrete production.
Our “flying” aggregate weighing system eliminates the need to add extra cement to the mix design to compensate for inaccurate weighing and dosing.
- More accurate weighing
- Less cement
- Correct slump
Tecwill’s modular construction makes the concrete plant fast to
install and easy to adapt
to a precast factory layout.

- All kinds of precast elements
- Blocks and paving stones
- Hallow-core slabs
- Masonry elements
Frequently asked questions
These are questions we’re often asked. We hope you find these helpful.
If you still have a question we haven’t addressed, please contact us directly.
Traditionally, a planetary countercurrent mixer is used to make precast concrete. This is the best option because of mixing efficiency. It is easy to put several discharge hatches in the planetary mixer, for example, due to the shuttle system for the drain washing water. Maintenance is also easy thanks to the large deck hatches.
Tecwill precast concrete plants are equipped with a durable and high-quality planetary countercurrent mixer. The mixer features:
- A homogenous mix with a shorter mixing time
- Easy maintenance with large service doors
- Wide range of options, including moisture and temperature probes, a high-pressure cleaning system, sampling and mixer camera
- Multiple discharge gate options
The most suitable method is determined by the size of the precast factory. At a small factory, concrete can be moved in a casting hopper by a bridge crane.
In a larger factory, a casting hopper is too slow. A shuttle and track system are needed to move the concrete from the mixer to the casting points.
There may be several casting points at a large factory – some fixed and others mobile casting machines – to produce hollow-core slabs, for example.
When manufacturing, each batch is poured into the precast element or concrete products. If the amount of water in the concrete batch is incorrect, elements will have a tone or quality variation manifested as a difference in color or strength, for example.
Accurate aggregate moisture measurement and the right water amount in the batch will reduce quality issues with the concrete.
Self-consolidated concrete or self-compacting concrete (SCC) is a highly “liquid” mix that flows easily and compacts under its own weight. A high-range superplasticizer (water-reducing admixture) is used in the mix.
The traditional mixing method is to first mix the dry ingredients – cement and aggregate – and adjust the batch moisture. Then, water and a superplasticizer are added. The mixing time of this method is very long, reducing plant capacity and increasing wear on the mixer.
Tecwill’s wet method improves moisture control. The artificial intelligence-controlled dosing and weighing ensure accurate amounts of materials for each concrete batch. The mixing uses the so-called “wet mixing” method, which shortens mixing time and improves capacity.
Tecwill in brief
- 30 years of experience designing and manufacturing concrete plants
- Our technology significantly reduces CO2 emissions from concrete production
- Global operations
- Head office, assembly factory and testing facility in Joensuu, Finland
Want more information?
Watch the Arcamix concrete plant delivery and operation video.
Watch the videoThe brochure gives more information about the precast concrete models, features, benefits and accessories.
Download the brochureWatch the fully automatic shuttle (flying bucket) system operation video.
Watch the video