In precast element manufacturing, the efficiency of concrete distribution is pivotal. The bucket conveyor system is vital to precast concrete production, ensuring the smooth progression of operations. In this article, we delve into the details of concrete transportation to explore the essential components, the critical role of planning and the importance of technology.
What does a bucket conveyor system include?
A flying bucket conveyor system for a precast plant is comprised of rail lines, conveyor buckets, plus any associated equipment. The system includes concrete discharge points, washing stations for buckets, a control system, a distribution system to multiple casting points in the factory and connections to casting machines.
Typically, an electric motor drives the flying bucket. The bucket speed is controlled by variable speed drive control. Over very short distances, other power supply options are also possible.
The conveyor bucket moves on either one or two rails. With one rail, the bucket may swing laterally. Therefore, the more robust two-rail version is commonly preferred.
The rail system itself is either attached to the pillars of the production hall or supported by a separate steel construction. This is often required in old precast concrete plants if existing structures cannot bear the additional load. Note that the rail system may include curves, upward and downward slopes and even crossings.
The bucket is the key element of the entire concrete transportation system. The bucket is discharged either by rotation or by opening a bottom hatch. A rotating bucket is well suited for long distances and larger volumes. Discharging through the bottom hatch is optimal for short distances and smaller buckets.
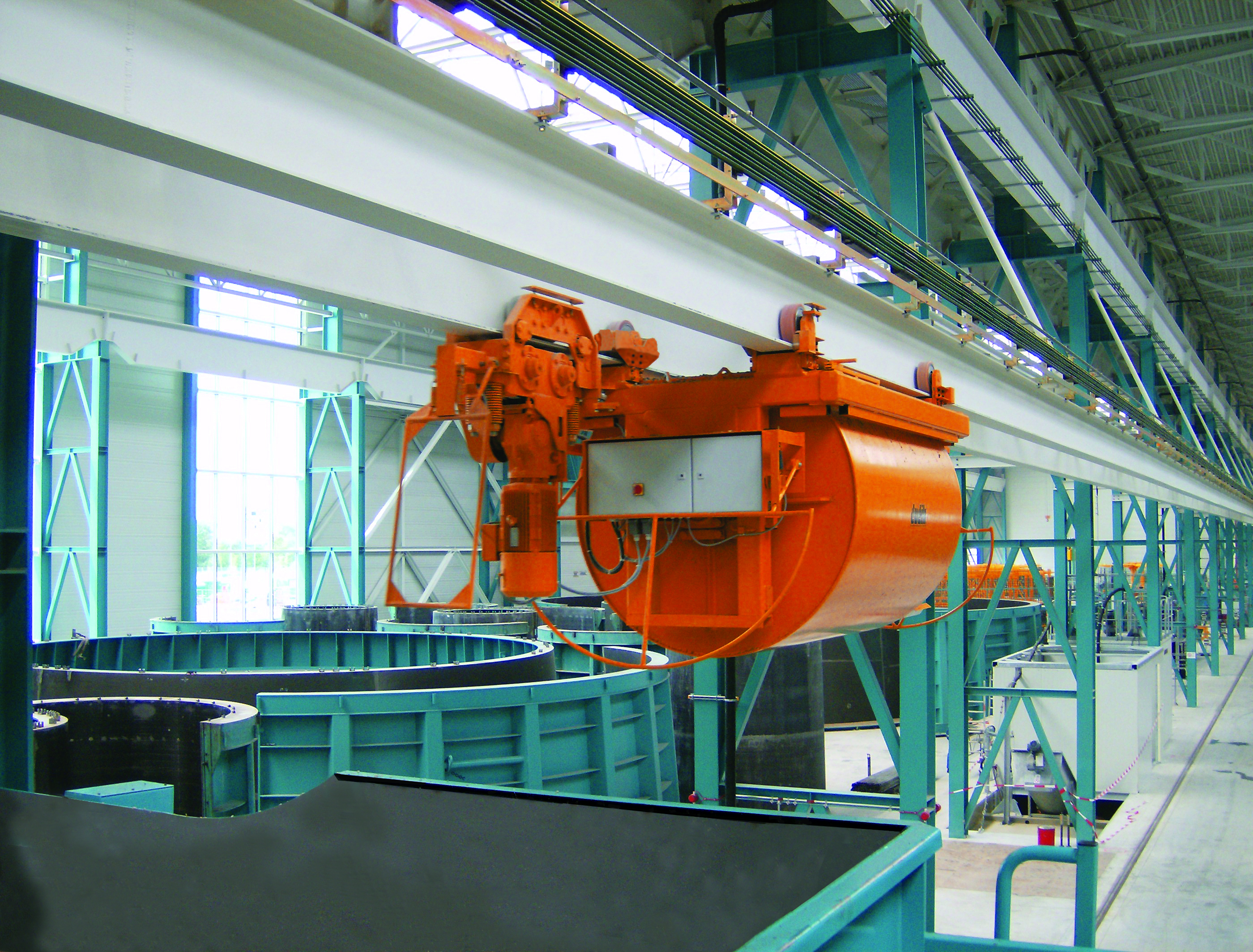
How is the conveyor controlled?
The control system is an essential part of the bucket conveyor setup for precast element plants. It handles the concrete orders from any order points and controls moving the bucket to desired discharge points.
A modern control system works almost completely automatically. It independently adjusts the concrete moisture and any other necessary parameters and places all orders received in an order queue.
The control system consists of a computer and stationary or portable order panels in various locations throughout the precast plant. The system operates wirelessly from portable devices in the WLAN network.
Reliability of the control system is crucial for continuous production without unnecessary downtimes.
Bucket conveyor with bottom hatch discharge.
How does concrete ordering happen?
A concrete order can be made from any of several stationary or portable order points. Today, orders are mainly handled wirelessly from portable devices.
If necessary, orders in the queue can be prioritized. Higher priority orders may be for casting machines, for example, as their operation needs to be continuous without interruptions.
An order can also be generated automatically. This happens when the control system is set to follow the casting process, evaluate the concrete consumption and ensure there is always enough concrete in the hopper of the casting machine.
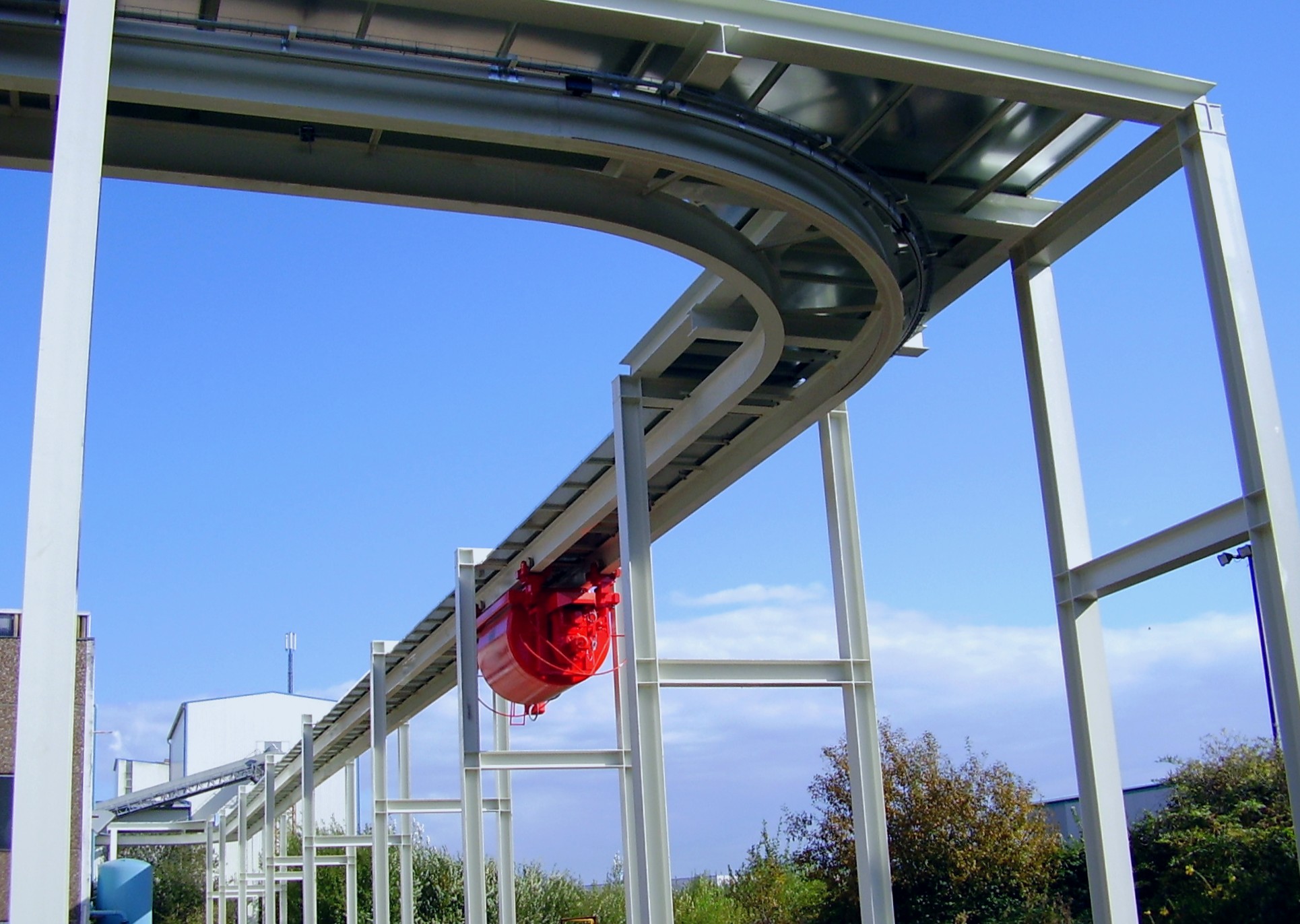
How are the concrete buckets cleaned?
Once the bucket is emptied, it moves to the cleaning station to be washed. This is done with a high-pressure washer, either manually or automatically.
A rotating bucket is turned into the discharging position, and the washer cleans the bucket from underneath. A bottom discharge bucket is washed from above.
Ideally, the cleaning station is also equipped with a water reclaim system. The system separates aggregates from the slurry water and pumps the water back to the concrete mixing plant. This reduces the amount of clean water required for concrete production.
Automatic bucket washing system in operation.
How big should the concrete distribution system be?
To dimension your concrete transportation system, begin by calculating how much concrete is needed at different casting points and at what frequency. The capacity of the concrete mixing plant must be taken into account, too. Once you know these, you can calculate the size of the bucket and speed of the conveyor to provide the required amount of concrete to each discharge point at precisely the right moment.
For larger plants, it is worth simulating concrete production and transportation in advance to ensure proper dimensioning. An under-dimensioned concrete transportation system may slow the casting process down or even stop operation of the casting machines.
Bucket conveyor system serving a casting machine.
What costs should be considered when investing in a bucket conveyor system?
When investing in a concrete transportation system for a precast plant, careful planning is necessary. Planning has a major impact on the system’s effectiveness and long-term success. Then again, planning costs are very low compared to equipment costs. We at Tecwill say, “Well planned is half finished.”
For a new plant, the investment should include the rail system, power supply, buckets, control system, order system, receiving hoppers and bucket washing system.
Installation costs include expenses for mechanical and electrical setup, as well as the construction work. However, you have the option to either have your own personnel install everything under the supplier’s supervision or opt for a turnkey installation.
Designing for existing precast plants
Designing a bucket conveyor system for an existing precast concrete plant comes with its unique set of challenges.
Older facilities often have structural limitations that affect the system’s design and implementation. Furthermore, if the existing concrete mixing plant already has issues due to inaccurate dosing or poor mixing, additional obstacles may arise. These may include insufficient capacity or inconsistent concrete quality.
Tecwill concrete distribution systems
Tecwill’s bucket conveyor systems are suitable for all – small or large, new or existing precast plants. Every Tecwill’s delivery includes a modern control system, order systems and a bucket washing system.
Whether for new or existing plants, efficient operation of all bucket conveyor components ensures a steady flow of concrete. After all, this is what empowers precast concrete manufacturers to meet their production goals with confidence, high quality and precision.
If you need additional details, feel free to reach out to us.
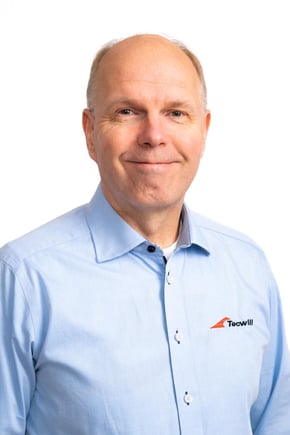