Fiber concrete production is often a cause of headache for concrete producers – especially when it comes to shotcrete production. Usually, fiber concrete is only needed for special projects. However, producing it requires the plant to be equipped accordingly. In this article, we will cover the main points important to producing high-quality fiber concrete for shotcrete purposes.
.jpg?width=1920&name=Spraying%20(2).jpg)
Raw materials and mix designs for fiber concrete
Fibers are typically used in concrete for reinforcement. They help to avoid cracks in the hardened concrete or increase concrete resistance against fire. The most commonly used fibers are steel, plastic, glass fibers and polypropylene.
When producing fiber concrete for shotcrete purposes, it is essential to use materials of only high quality and constant composition.
The maximum aggregate size for shotcrete production is ¼ inch (8–10 mm). Larger grains may get stuck in the nozzles during spraying.
The amount of cement required for fiber concrete production is quite high, sometimes even up to 500 kg/m3. To replace some of the cement, different binders, such as microsilica or limestone powder, are often used.
The water-cement (w/c) ratio is usually below 0.45. This means that it is almost impossible to get acceptable concrete workability without adding chemicals. Only with the right amount of suitable admixtures can fiber concrete become optimal for pumping and spraying.
In addition, an accelerator needs to be added to the concrete in the spraying machine. The accelerator speeds up the solidification and hardening process. This improves the ability of concrete to stick to the walls and ceilings.
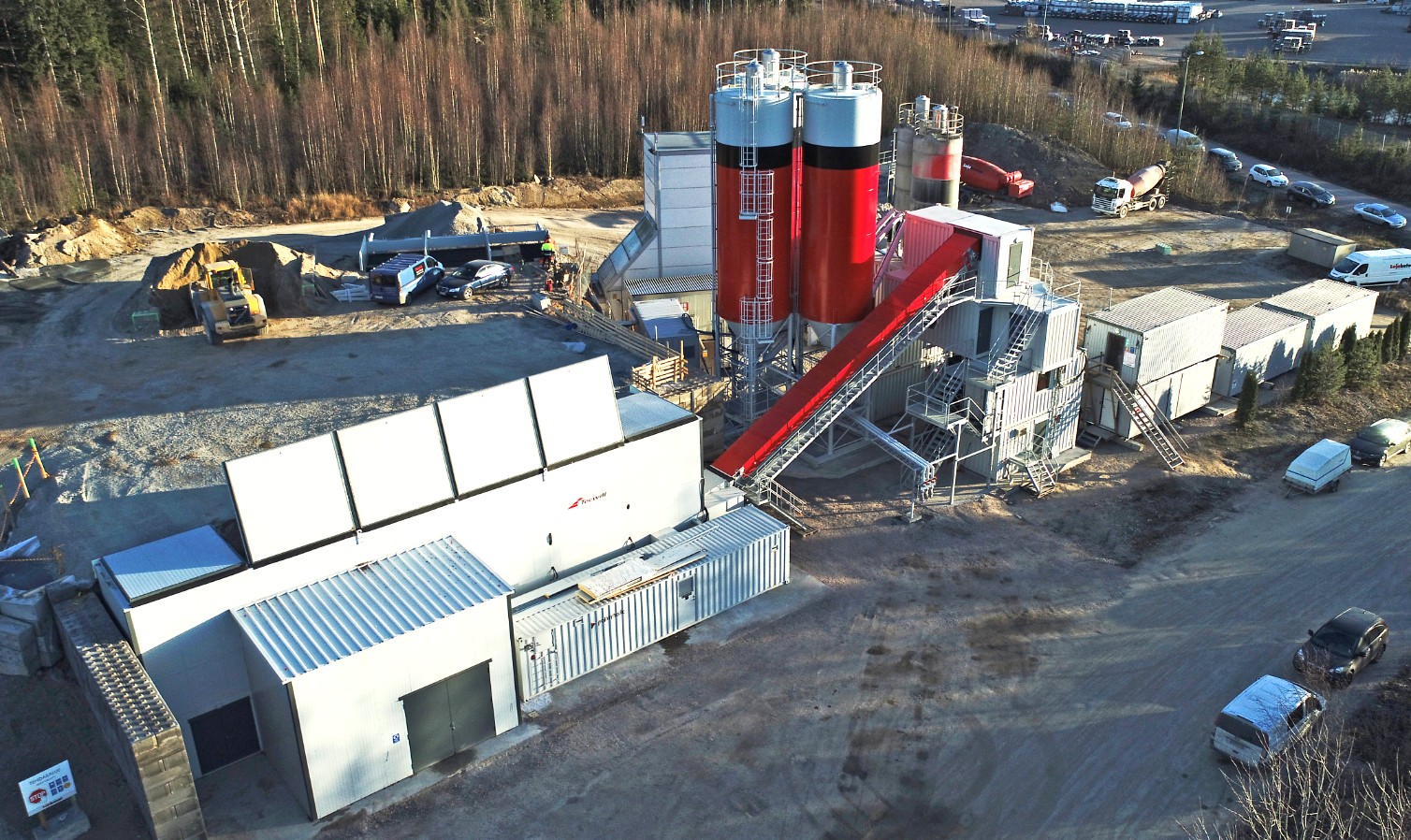
What to consider at a concrete plant
Producing high-quality fiber concrete places certain demands on concrete plants.
First of all, accurate dosing devices and weighing systems are absolutely essential. From batch to batch, the dosing deviation should be as low as possible. If there is a high variation in aggregates, there is also a high variation in the amount of binders and water required in a mix.
Secondly, the aggregate moisture measurement must be done automatically. This includes the calculation of the water reduction from the batch water. Especially for mixes with a low water-binder ratio, even a small mistake in the calculation caused by a wrong aggregate moisture value will affect the quality of concrete.
Inaccurate dosing or moisture measurement both have a negative impact on workability and solidification when spraying shotcrete. However, detecting these issues is only possible with laboratory tests.
Other important factors are the control system and the mixer. The control system must be able to take care of accurate dosing of all the ingredients, precise aggregate moisture measurement and automatic control of the water-binder ratio and concrete consistency.
The mixers most perfectly suited to mix fiber concrete are, for example, planetary countercurrent mixers or twin-shaft mixers.
Maintaining stable fiber concrete or shotcrete temperature is extremely important, too. Any temperature variations affect the concrete hardening process. Plus, these can be easily seen, for instance, when spraying concrete for the tunnel lining. Therefore, automatic concrete temperature adjustment is essential for the aggregate and water heating system and the plant’s batch control system. Concrete temperature must be measured and documented within the batch control system.
.jpg?width=1802&name=SteelFiberDosing%20(2).jpg)
Pros and cons of different fiber dosing methods
1. Dosing fibers into the concrete truck mixer’s drum
After the concrete has been discharged into the truck mixer’s drum, the truck drives to the fiber dosing station. There, fibers are added to the concrete – either manually or with a dosing belt conveyor.
Pros
- Concrete mixing with the concrete plant’s mixer is fast
- No risk of fibers getting into non-fiber concrete mixes, as no fibers are left on the conveying equipment
Cons
- Adding fibers and mixing takes a long time
- Despite the longer mixing time, the concrete may still not be homogeneous, with fibers not equally spread throughout. As a result, there may be fiber clumps, which can get stuck in the hoses, pipes or nozzles
- This dosing method is not suitable for loose plastic fibers
2. Dosing fibers into the concrete plant’s mixer
Pros
- No risk of fibers getting into non-fiber concrete mixes
Cons
- A proper dosing device is necessary and sometimes challenging to accommodate
- Space for the dosing device is needed in the mixer area
- A longer mixing time is necessary, reducing the capacity of the concrete mixing plant
- Fiber clumps may still occur and can get stuck in hoses, pipes or nozzles
3. Dosing fibers at the end of the aggregate weighing belt or lifting conveyor
In most concrete plants, aggregate weighing is done by a weighing belt conveyor. In this case, it is possible to install the fiber dosing equipment next to the belt conveyor. This allows dosing the fibers on top of the aggregates.
Pros
- Fiber dosing on the belt conveyor is easier than into the concrete mixer
Cons
- Space for the dosing device and conveyor is needed in the aggregate bin unit area
- Dosing and mixing take longer, reducing the concrete mixing plant’s capacity
- Fiber clumps may still occur and can get stuck in hoses, pipes or nozzles
4. Dosing fibers on top of the aggregates flowing on the “flying” weighing belt conveyor
This method is only possible with Tecwill’s “flying” aggregate dosing and weighing system. In this case, an automatic fiber dosing system is installed next to the aggregate bin unit.
When the aggregates flow on the weighing belt conveyor, fibers are dosed continuously on top of the thin aggregate bed. This results in the premixing of fibers and aggregates before they reach the aggregate holding hopper.
Pros
- Fibers are mixed homogeneously; fiber clumps do not occur
- Short mixing time, not affecting the capacity of the concrete mixing plant
- Suitable for all fiber types
- Easy to connect to aggregate bins, even as a retrofit
Cons
- Some fibers might remain on the belt conveyor and may be mixed into a concrete batch for which they were not intended
.jpg?width=511&name=KuituAnnostelu%20(2).jpg)
Summary
Producing fiber concrete, especially for shotcrete purposes, requires consideration of many things at a concrete batching plant. It calls for only high-quality materials and the appropriate mix design. In addition, accurate dosing devices, low deviation from batch to batch, precise aggregate moisture measurement and an efficient mixer are all essential.
The fiber dosing method plays a role, too. After all, it may significantly affect the quality of concrete and the plant’s capacity.
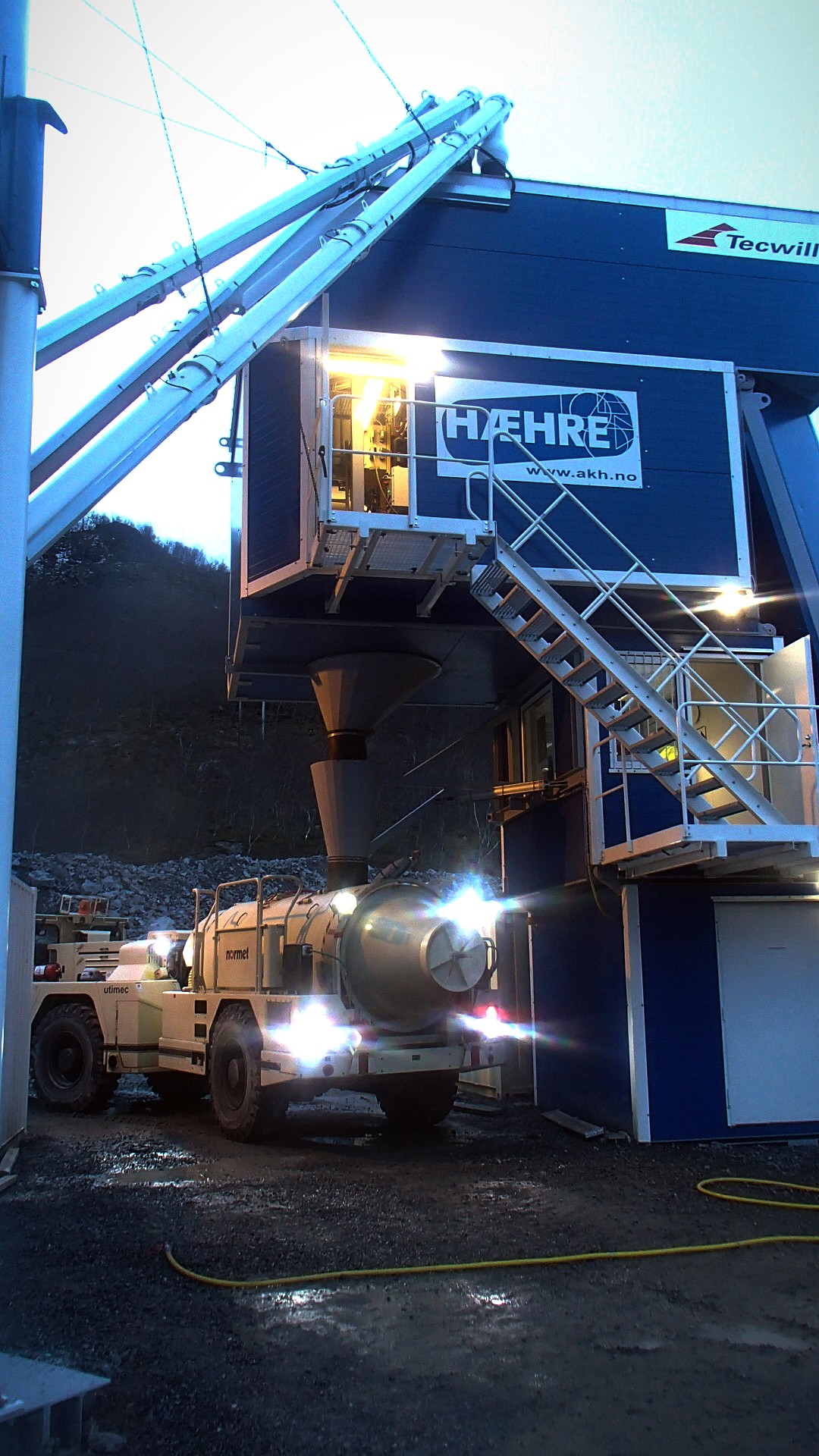
Tecwill’s solution for high-quality fiber concrete
Tecwill’s “flying” aggregate dosing and weighing system together with an automatic fiber dosing device is the best possible way to produce homogenous and high-quality fiber concrete. Importantly, it doesn’t decrease the production capacity of the concrete mixing plant.
If you want to receive more information, we are happy to answer all your questions.
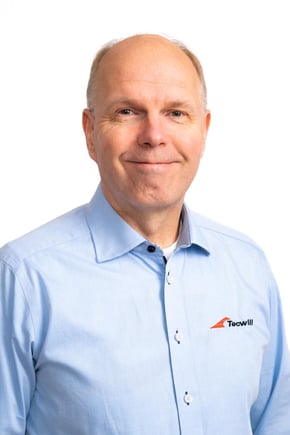