Shotcrete – or sprayed concrete – plays a pivotal role in ensuring the safety and functionality of mining tunnels. In this blog, we’ll delve into the methods and machinery involved in shotcrete production. We’ll also discuss the critical role of high-quality shotcrete plants and mixers. The consequences of making the wrong choices in tunnel construction will also be covered.
How to ensure concrete logistics for the mining tunnel?
There are several ways of ensuring concrete logistics down to a tunnel. All of them have different impacts on the production process and the operational costs. Let’s delve into them extensively.
1. Gage
The most logistically irrational and expensive option is to use a gage. If the gage size is small, it will be difficult, slow and impractical to get the plant modules and all necessary materials down where they are needed.
2. Spiral road
A spiral road is a road going down in continuous bends. The length of the spiral road depends on the depth of the tunnel below ground.
The spiral road is a practical choice for tunnel logistics because it allows transportation by trucks. It makes it quite easy to transport the modules of the concrete batch plant, binders, aggregates and other materials down to the tunnel.
3. Slickline
A slickline is a metallic pipe installed in a hole drilled through the rock. Such a pipe can be up to a kilometer long and with a diameter of 100–150 mm (4–6”).
If shotcrete is produced above the ground, it can be dropped down through the slickline to a receiving hopper in the tunnel. From the hopper, the shotcrete is transported to the spraying area by a suitable underground transmixer or agitator.
One drawback associated with this approach is the potential for shotcrete segregation during the dropping process. Such segregation can have adverse effects on shotcrete quality and sprayability.
If shotcrete is produced underground, a slickline can be used to transport aggregate raw materials. Cement, however, needs to be transported in big bags. In this case, all materials can be mixed as usual in an underground concrete mixing plant – with no negative impact on shotcrete quality or sprayability.
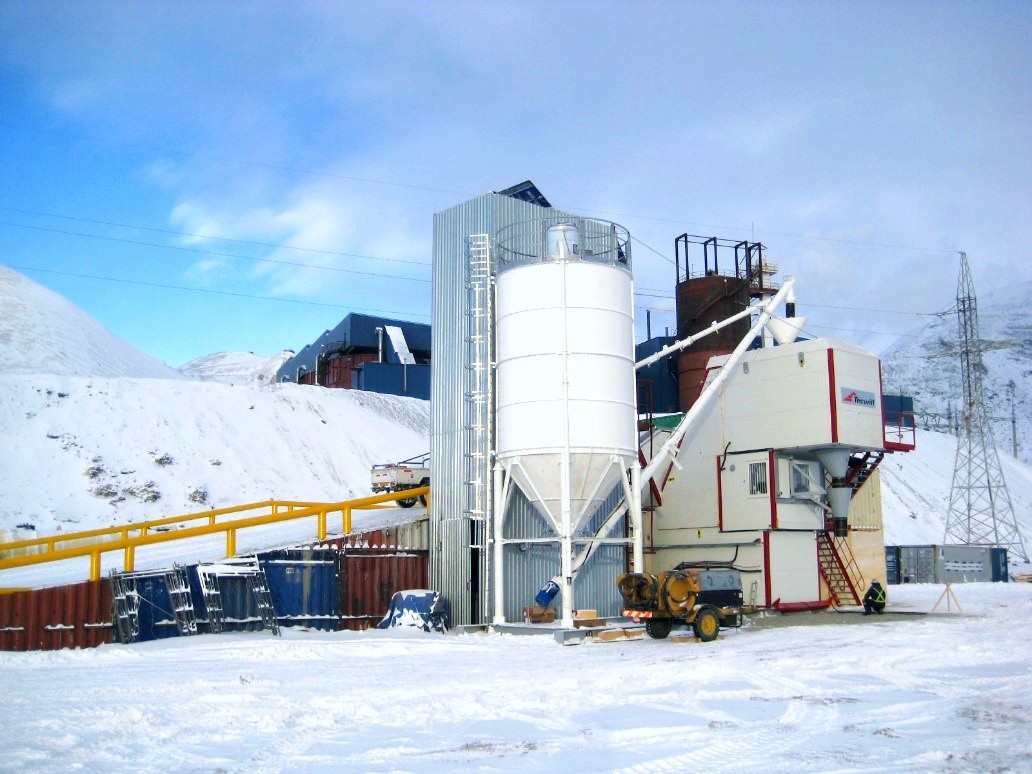
How shotcrete can be produced?
Concrete for shotcrete purposes can be mixed on either the ground level or underground in a tunnel. There are considerable differences between these two options.
Mixing concrete on the ground level
The best method to mix shotcrete is using a standard concrete mixing plant, as with any other concrete mix design. For example, Tecwill’s Cobra plants are widely used for this purpose.
Nevertheless, for a concrete batch plant to effectively handle shotcrete, it must be equipped with a high-accuracy material dosing and weighing system. Plus, a potential dispensing system for steel, synthetic or polypropylene fibers is also preferable.
Precision in material dosing and moisture control is crucial. Even minor mistakes in material quantities can result in an inaccurate water-cement ratio and an improper slump. This will ruin the shotcrete quality and create issues at the spraying point.
Another alternative for ground-level production entails the utilization of dry pre-blended shotcrete.
To make it, cement, aggregates and admixtures are mixed together and discharged into super bags at the dry-mix plant. Normally, such super bags can weigh up to 1,500 kg (3,300 lb). The bags are then transported from the dry-mix plant to the tunnel, where the material is mixed with water.
Sometimes, the distance between the plant and the mine is several thousand kilometers. Moreover, storing the bags is challenging as potential humidity can lead to the hardening of their content.
In addition, drying of aggregates requires a lot of energy and generates considerable CO2 emissions. These are the reasons why using dry pre-blended shotcrete is a very expensive method. It can cost even USD 500 per cubic meter and more.
Mixing concrete underground
Another option is to mix all the materials underground, close to the spraying area. In this case, less cement is required, and the shotcrete quality will be much better.
It’s also much cheaper to produce shotcrete right underground. However, the costs of getting all the materials down to the plant need to be considered.
Specially designed underground sprayed concrete plants are suitable for mixing shotcrete in tunnels. They can homogenously mix aggregates, cement, water and admixtures according to the actual mix design. If necessary, different kinds of fibers can be dosed as well.
Benefits of underground mixing:
- Shotcrete is homogenous – better slump
- Less cement required
- Higher early strength
- Short distance between mixing and spraying areas
- Fibers can be mixed in homogeneously
- Cheaper production compared to using dry pre-blended shotcrete
- Reduced energy and CO2 emissions
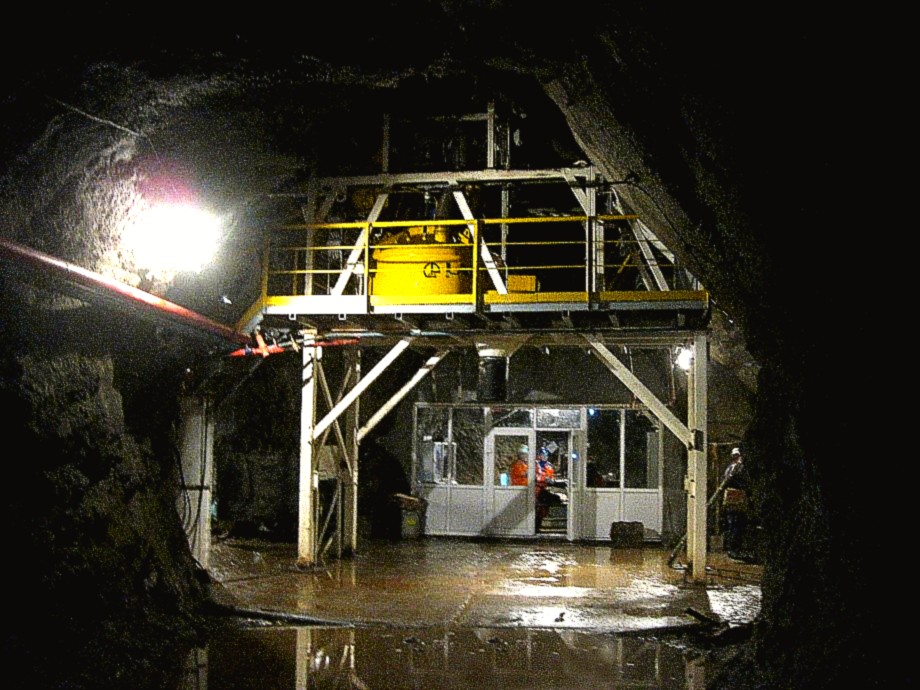
below the ground level.
What types of mixers are used for shotcrete?
For mixing shotcrete, either continuous auger (screw) or planetary countercurrent mixers are used.
Continuous mixers
With a continuous mixer, the shotcrete consistency, quality and early strength might vary in every batch. This is because water will not be added to the mix equally every time. Some concrete might even have to be dumped due to its poor quality.
Moreover, it’s very challenging – or even impossible – to add fibers to the mix when using a continuous mixer. Clumps of fibers can then lead to problems with the spraying machine and the sprayed concrete lining the tunnel walls.
Planetary countercurrent mixers
With a planetary countercurrent mixer, aggregates, cement, water, admixtures and fibers can be dosed separately. Therefore, all ingredients will be mixed properly.
In this case, the shotcrete quality will be better, whereas early strength higher and more consistent. Plus, much less cement will be required.
What are the requirements for an underground shotcrete plant?
First, the plant modules have to reach the underground area. As mentioned earlier, there are different methods to ensure this.
Second, when designing a shotcrete plant, consider the limited space of a tunnel. Note that some extra space is required also around the plant so that all the materials can be loaded into bins, silos and tanks – and shotcrete discharged.
Third, proper mixing is important to ensure that the shotcrete is as homogeneous as possible. Low-quality shotcrete not only reduces the efficiency of the construction work but also leads to higher costs. Additionally, it increases the risk of failures of the tunnel wall linings, impacting tunnel safety.
Finally yet importantly, adding fibers and different admixtures to the mix is very important in shotcrete production.
Suitable admixtures ensure that shotcrete can be transported, pumped and sprayed easily – even after a longer transportation time. Fibers, in turn, can significantly enhance the structural integrity of the shotcrete. They help in reducing cracking and improving the overall durability of the tunnel lining. This is why a sophisticated and reliable dosing and mixing system should be considered.
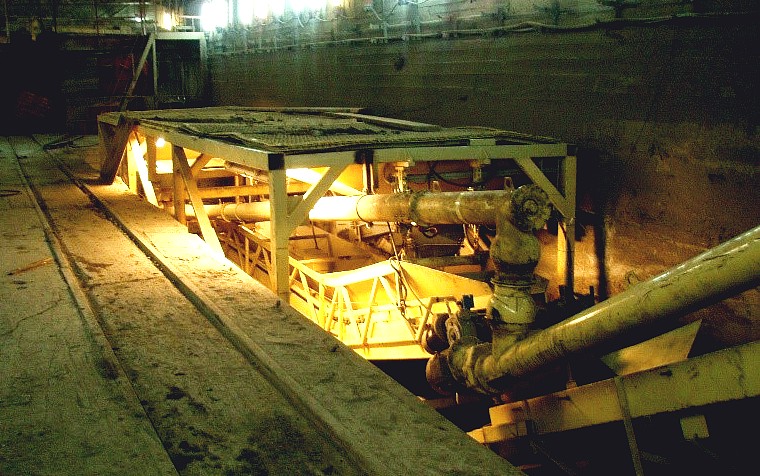
Risks associated with poor shotcrete plant choices
Investing in a high-quality shotcrete plant with the appropriate mixer is a decision of paramount importance. The consequences of a wrong choice can lead to substantial financial losses. To illustrate, here are a few examples:
- Poor-quality shotcrete increases the risk of stones or shotcrete lining falling from the tunnel walls
- Areas sprayed with poor-quality shotcrete might have to be taken down and replaced
- Fiber clumps in the mix might get stuck in hoses or nozzles. This increases the risk of potential equipment damage during the concrete spraying process
.jpg)
Tecwill’s shotcrete plants
Depending on project requirements, Tecwill can provide shotcrete plants designed for both above-ground and underground production. The plants feature high-quality countercurrent planetary mixers to ensure the best possible mixing result. In addition, fully automatic fiber dosing systems can be provided.
Tecwill’s wide range of solutions is proven to deliver cost-effective operations. They improve safety in the tunnels, decrease cement use and reduce the environmental impact of a project.
If you have any other questions about Tecwill’s shotcrete plants, feel free to contact us.
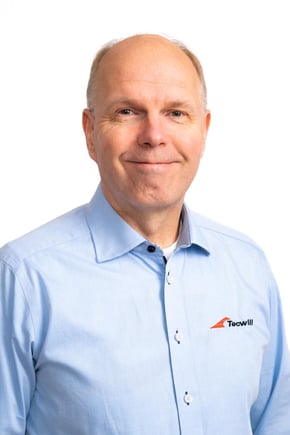