The heart of a concrete batching plant lies in the mixer. Understanding the essence of a successful mixing result is important in choosing the best mixer. This article explores the various types of mixers, control methods and the importance of maintenance and safety.
Concrete mixer types
The mixer turns raw materials into a product of value: concrete. Often, the mixer even determines the layout of the whole concrete mixing plant. This is because to achieve the highest mixer user-friendliness and production capacity, everything in the plant must be dimensioned to fit the mixer. This includes the transport and dosing equipment, scales and all the rest.
The modern mixer market is vast with a wide range of mixer types and models. The most common ones are:
- Countercurrent planetary mixer
- Free-fall drum mixer
- Single-shaft mixer
- Twin-shaft mixer
Each concrete mixer has its own properties and characteristics. These include dimensions, volume, power, weight, mixing technology and application. No matter what kind of mixer a plant has, efficiency factors apply to all.Inner workings of a twin-shaft mixer.
Mixing efficiency is central
Concrete mixer efficiency has a big impact on how well cement, water and additives can be homogenized with aggregates.
Intense, efficient mixing is required to reach good concrete workability, compressive strength, impermeability and even frost resistance.
However, efficient doesn’t always mean super quick. A variety of factors affect mixing time. These include the concrete mix design, raw materials used, specifications of the relevant standards, mixer type, condition of the mixing tools and the batch size. Generally, mixing time varies between 30 and 120 seconds.
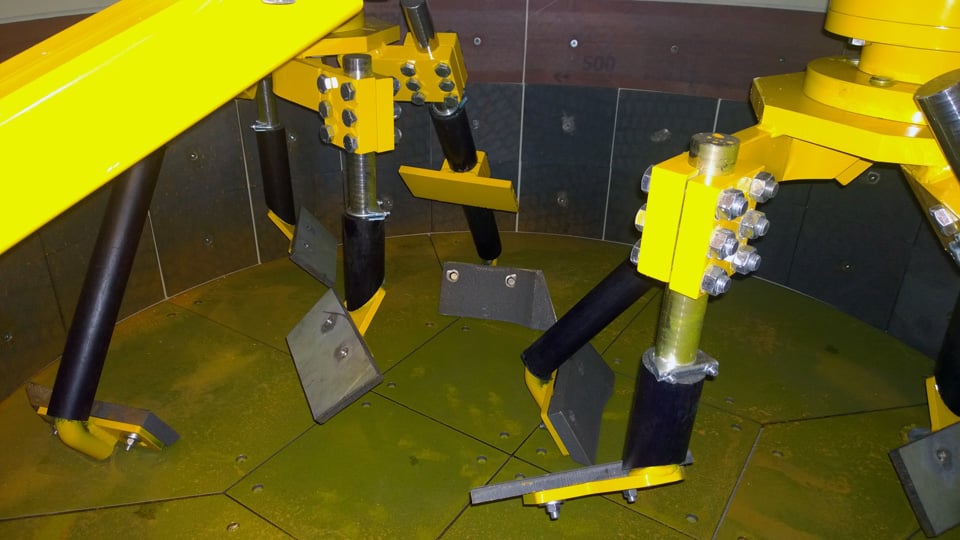
Ways to control the mixing process
The operation and efficiency of the mixer depend a lot on how well it is taken care of. Some parameters can be controlled and adjusted by the plant’s operator. These are:
- Sequence of scale emptying
- Waiting time between mixing and discharging of different materials
- Position and condition of the mixing arms. Occasional mechanical adjustment minimizes mixing arm wear and helps maintain mixing efficiency
- Total mixing time
- Mixing arm speed if the mixer motor is equipped with frequency inverters
For closer control, the mixing process can be monitored with an HD camera in a dust-proof housing installed on the mixer or by following displays on the control screens. These can provide a good indication of how homogenous the concrete is. Plus, mixers are often equipped with an inspection hatch, allowing a look inside the mixer during the process.
Nevertheless, defining the best mixing process for a specific concrete mix design requires testing both fresh and hard concrete.
Maintenance and safety
Maintenance and safety factors are essential for efficient production.
Mixer motors range from 15–75 kilowatts. If two or three motors are in use, the power can even reach several hundred kilowatts. This generates enormous power inside the mixer – but also can lead to increased risks during operation.
Adhering to safety regulations and operating instructions is paramount.
Carrying out preventive maintenance as specified by the mixer manufacturer is necessary. Manufacturer recommendations should be followed even if the mixer’s actual operating hours displayed by the control system don’t seem high.
Mixing arms’ movement in a twin-shaft and countercurrent mixer.
Partnering for success
Choosing the right concrete mixer can be a daunting task, given the market’s versatility. Partnering with a knowledgeable expert can help in the successful navigation of this process.
Tecwill offers a wide range of versatile mixing solutions for different types of concrete. These include:
- Ready-mixed concrete
- Shotcrete, high-quality wet concrete
- Self-compacting concrete (SCC)
- Ultra-high-performance concrete (UHPC) for precast plants
- Earth-moist concrete for block and paver factories
Even with the best-in-class mixer, achieving all desired concrete properties is only possible if the materials are dosed according to the mix design and as accurately as possible. The weighing accuracy of the scales and precision of the dosing equipment should be repetitive and of the highest level.
Tecwill’s WillControl control system comes in handy for this purpose. The system helps achieve excellent repeating precision. It allows discharging various raw materials into the mixer in the exactly specified amount, order and time. And what is more, it anticipates the need for the maintenance of the mixer and other plant equipment, ensuring continuous production efficiency.
For further information, please contact Teemu Tuominen.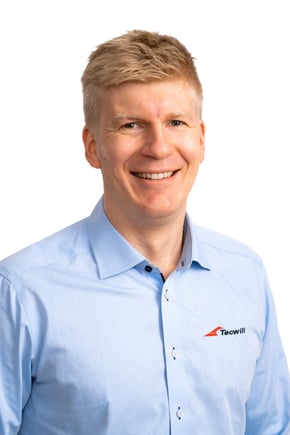