Inaccurate measuring of aggregate moisture increases production costs
One of the biggest challenges in concrete production is variation in aggregate moisture content. It is highly important to make regular aggregate moisture measurements. But how can they be made accurately and easily – and how can you choose the right kind of solution? Let’s discuss this below.
Lack of real-time moisture measurement increases production costs
Aggregate moisture content – the percentage of water contained in the aggregates – greatly affects the quality of a concrete mix.
Let’s say a 4 cubic yard (3 m3) concrete batch with 13,000 lb. (6,000 kg) of aggregates has a moisture content of 4%. This means 520 lb. (240 kg) of water are contained in the aggregates. Given that deviation in the aggregate moisture measurement is +-1%, the variation of aggregate water content is +-130 lb. (+-60 kg).
A variation like this can be compensated for by manually increasing or reducing water based on the data from the ampere meter, which shows the power being used by the mixer motor(s). However, manual adjustment leads to inconsistency in concrete quality, increases dosing and mixing times, reduces production capacity and can even generate unnecessary wear on the mixer, all of which highly affect overall production costs.
To maintain the right amount of moisture in each batch, real-time aggregate moisture information is needed. Only then can the right amount of water be added to the mix to achieve the targeted result.
Moisture measuring probes
A moisture sensor or probe can facilitate the systematic assessment of aggregate. Several types of moisture measurement sensors and probes are available on the market, each with its pros and cons – and the ultimate price. Let’s discuss the three most common ones in detail.
1. Radar sensors
- Measurements based on radar technology
- Up to 0.1% accuracy
- For aggregates with a moisture content of 0–90%
- Accurate measurements even when aggregates are exposed to steam in winter or when they differ in size
- Operates for long periods using automatic measurement compensation without the need to recalibrate, even in the event of sensor head abrasion
- The sensor head can be easily changed; dismantling is unnecessary
- The sensor can conduct up to 15 calibration curves itself; therefore, external evaluation devices are usually not required
- Easy connection to any currently existing batch control system
- Can be used as a “skid” type of sensor for the Tecwill “flying” aggregate weighing and dosing system
2. Microwave sensors
- Measurements based on microwave technology
- Up to 0.3% accuracy
- For aggregates with a moisture content of 0–15%
- Properly recalibrated sensors provide accurate measurements even if aggregates are exposed to steam in winter
- In the event of progressive sensor head abrasion or any notable change in the aggregate grain curve, recalibration is required
- The sensor head can be changed easily; dismantling is unnecessary
- Easy connection to any currently existing batch control system
- Can be used as a “skid” type of sensor for the Tecwill “flying” aggregate weighing and dosing system
3. Optical sensors
- Measurements based on optical technology (led light)
- Up to 0.3% accuracy
- For aggregates with a moisture content of 1–20%
- Require more space than other sensors with a measuring distance of 3 - 5 feet (0.6 – 1.6 m)
- Measurement results may not be accurate if the sensor head is dirty, or the environment is dusty or steamy
- Sensor calibration is more difficult
- Easy connection to any currently existing batch control system
With any sensor, measuring results can vary greatly. This creates the assumption the sensor is unreliable. Typically, the sensor is not the problem. Other factors are affecting the results. These include the aggregate dosing system in use, the sensor’s location and even improper calibration.
Let’s look at one often-overlooked factor below.
Moisture probe installation locations
Sensor location makes a difference. Moisture measurement sensors are typically installed in one of four spots in a concrete mixing plant. Let’s discuss how they differ.
1. Installation in the aggregate bin cone
Sensor is installed with the sensor head protruding into a bin cone.
- The sensor head protrudes into a bin cone
- Moisture measurements can be inaccurate due to measuring only material close to the cone wall
- The sensor is not visible, and its calibration is quite difficult
- The sensor wears out, and its actual condition is difficult to check
- An expensive solution, as each aggregate bin needs a sensor
2. Installation underneath a dosing gate at the bottom of the bin cone
Sensor is installed under a dosing gate measuring the moisture of the aggregates falling onto the weighing belt conveyor.
- The sensor measures the moisture of the aggregates falling onto the weighing belt conveyor
- Reduced measuring accuracy due to inconsistent amounts of material falling from the bin
- High wear of the sensor head
- The sensor is visible, and it is easier to check its condition
- An expensive solution, as each aggregate bin needs a sensor
3. Installation at the bin outlet above a belt feeder
Sensor is installed at the bin outlet above a belt feeder measuring the moisture of the aggregates flowing from the bin with the moving of the belt conveyor.
- The sensor measures the moisture of the aggregates flowing from the bin on the belt conveyor
- Higher measuring accuracy due to material steadily flowing out of the outlet
- High sensor head wear
- The sensor is visible, and it is easier to check its condition
- An expensive solution, as each aggregate bin needs a sensor
4. Sensor installed above the weighing belt conveyor
Skid-probe is mounted above the weighing belt conveyor, during the dosing process flowing on top of the aggregate bed, measuring the moisture of each aggregate fraction one after the other for the next batch (only possible in connection with the Tecwill “flying” aggregate dosing and weighing system!)
- The sensor measures each aggregate fraction flowing on top of the aggregate bed
during the dosing process - Easy to check the condition of the sensor and replace worn heads
- Easy to calibrate and recalibrate, as required
- Both optical and microwave probe can be used
- Economical solution since all aggregates are measured by only one sensor
- Only available for the “flying” aggregate weighing and dosing system
Summary
All types of sensors have their own pros and cons. Depending on specific factors, the accuracy of all measuring devices varies. All require calibration – and most even require recalibration.
Yet to ensure the best possible performance of any sensor, it is very important to install it correctly.
The final price always depends on the cost of the system itself, the number of probes required and installation and calibration costs. The most economical option is to have just one sensor, which is only possible if it’s installed above the weighing belt.
Learn more about concrete plant solutions >
Tecwill approach to moisture measurement
Tecwill uses a “flying” aggregate dosing and weighing system with "OptiMoist" moisture measuring system.
The “flying” system represents green technology in concrete mixing. It not only lowers investment and installation costs but also helps reduce the use of cement and, therefore, CO2 emissions.
The “flying” system is the only one to allow one combined OptiMoist probe for all different aggregate fractions. The probe can be either a “skid” type or optical non-contacting. The sensor accurately and continuously measures the moisture of all aggregates dosed for the batch along the aggregate bed. The probe can be calibrated to all aggregate fractions used at the concrete batch plant.
For further information, read more about Tecwill’s “flying” weighing system or contact our team.
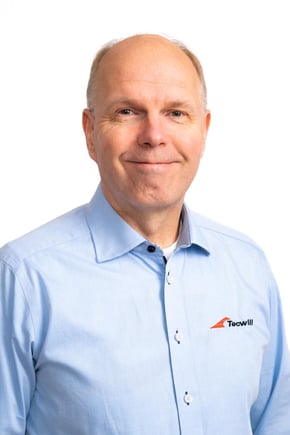