Flying weighing
Reduced operational costs with the Tecwill “flying” aggregate dosing and weighing system
The “flying” aggregate dosing and weighing system reduces the operational costs of concrete production. Dosing with a variable-speed drive brings dosing accuracy by down to 2 kg and improves weighing deviation. The improved Tecwill OptiMoist aggregate moisture measuring system enables the correctly calculated water dose for the batch.
- Better aggregate dosing accuracy by down to 2 kg (4 lb)
- Possibility to save cement by up to 30 kg/m3 (50 lb/yd3)
- Short weighing time and increased plant capacity
Enables 2–5 m (6–15 ft) lower aggregate bin filling level
Dynamic “flying” weighing conveyor requires very limited space. The aggregate bin construction can be 2–5 m (6–15 ft) lower than a conventional weighing belt solution. This saves space at the site.
- 2–5 m (6–15 ft) lower aggregate bin filling level
- Lower filling ramp saves space at the site
- Significant savings in fuel and wheel loader operating costs
Allows a simple and low-cost steel skid foundation for mobile solutions
Thanks to the “flying” aggregate weighing system with a low-profile aggregate bin foundation, is very easy to make. Underground construction is not needed. Only a simple flat concrete slab is enough for a stationary installation.
In a mobile setup, the plant is equipped with a mobile steel skid foundation and aggregate bin loading ramp elements.
- Simple foundation
- Mobile steel skid foundation for mobile setup
- Filling ramp elements for bins come with the plant
- Fast installation, even in winter
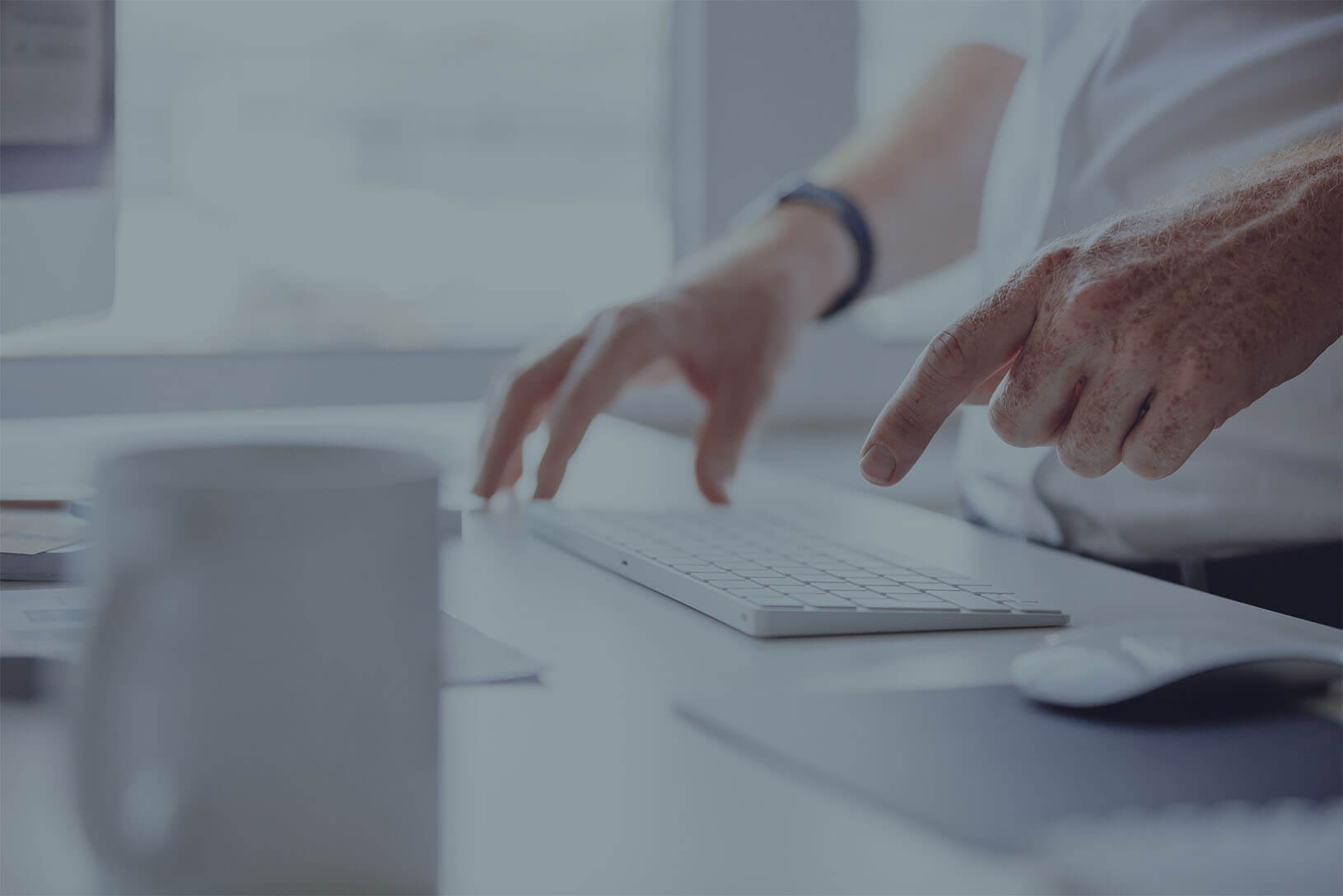