The concrete plant project in Lorenskog, Norway, presented a unique set of challenges, which tested our patience and redefined the boundaries of what our team could achieve.
Situated just outside the bustling Oslo city center in the suburb of Lorenskog, this concrete batch plant was expected to handle significant daily ready-mix concrete production volumes. Consequently, it was imperative for the new premix wet batch plant to have substantial capacity for both aggregate storage bins and cement silos.
However, when we first visited the customer’s site, we realized that the space available was quite narrow. The location was sandwiched between the road and existing buildings. Therefore, everything had to be planned thoroughly to address these spatial constraints.

Huge Arcamix wet batch plant for a small footprint
Together with the customer, we started to plan a suitable layout.
Given the limited space, we recognized that innovative solutions would be essential to maximize efficiency. Therefore, Tecwill’s Arcamix 4.0 modular concrete mixing plant with Vertec vertical aggregate lifting conveyor was chosen for the project.
Other challenges along the way
Even when the planning stage was completed, the further journey had its own share of challenges.
First, the customer encountered obstacles related to construction permits in the city area. It was only after getting all the necessary permissions that the installation of the plant could commence.
However, in March 2020, the whole world was put on hold by the COVID-19 pandemic. With travel restrictions and other measures, the coronavirus really tried everyone’s patience.
Despite all these challenges, the plant started up on time – even without our team members being there physically. This is something only possible with pre-assembled and factor-tested plants like Tecwill’s Arcamix.
The plant’s pre-wired and factory-installed modules were easy to install and connect with rapid connectors. This allowed for the successful launch of the plant even remotely.
The customer’s installation team carried out all installation works – with remote support from a Tecwill supervisor provided whenever they had questions.
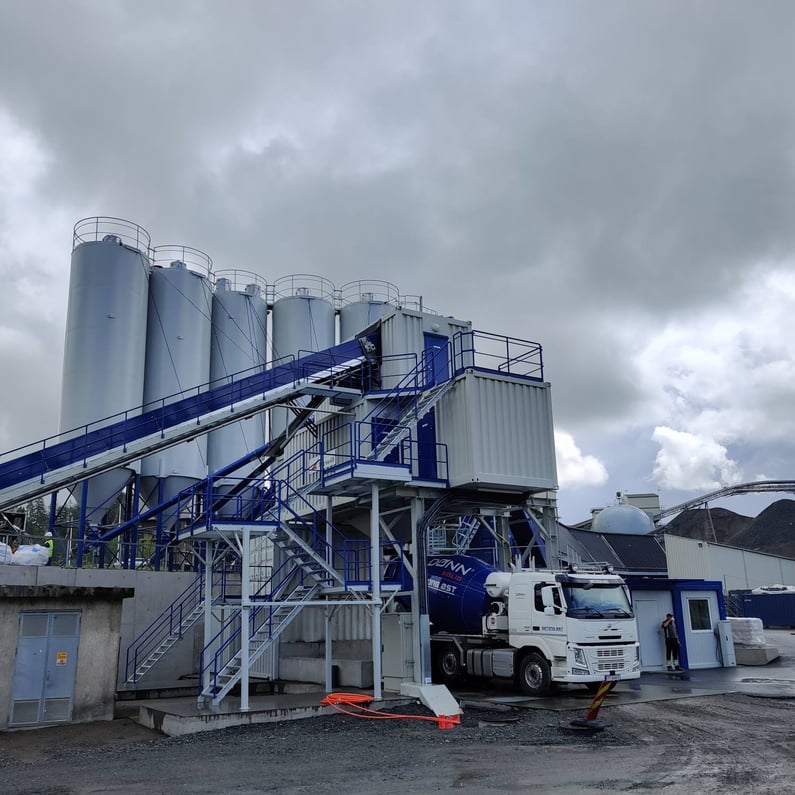
Advanced technology and vertical aggregate lifting
The Arcamix modular concrete plant delivered to Lorenskog boasted a wide range of cutting-edge features. For instance, it came with a highly effective “flying” aggregate dosing and weighing system for unparalleled precision in concrete production. The plant design has also included a robust 5.2 yd3 (4.0 m³) BHS high-quality twin-shaft mixer, water scales for clean and recycled water, as well as a high-pressure mixer washout system.
Most importantly, the plant integrated a compact Vertec vertical aggregate bin filling system. Well insulated for reliable operation in cold Nordic weather conditions, it was especially suitable due to its ability to operate on a small footprint.
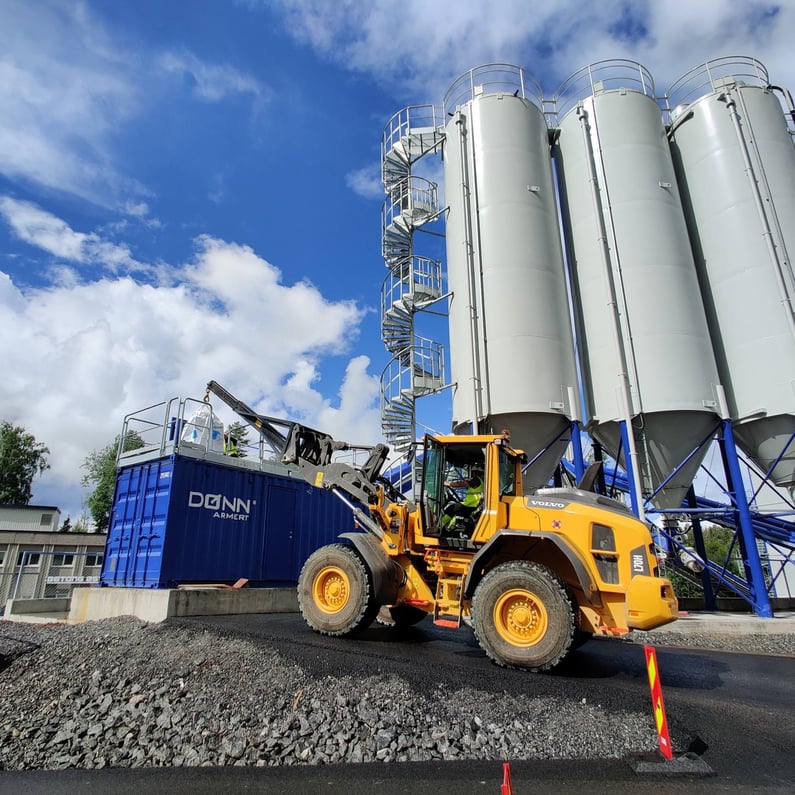
Fully automatic fiber dosing system
What is more, the delivery included a fully automatic fiber dosing system. Facilitating the precise dosing and transportation of fibers, the system played a critical role in this project.
Most commonly used in applications such as floor castings or tunnel shotcrete, fiber concrete reduces reliance on traditional reinforcement. It also minimizes the labor required for reinforcement work.
The system can dose steel fibers, synthetic macro-fibers and polypropylene fibers.
The operation of Lorenskog’s system is straightforward. After the fiber is dosed, it is lifted by a conveyor above the mixing unit. From there, it falls along the tube under the mixer into the discharge funnel.
Additionally, the fiber feeders are cleverly mounted on top of the scale sensors. This way, the control system automatically receives information about how much fiber has been dispensed.
In the end, this reference story not only exemplifies our ability to tackle complex projects but also demonstrates the resilience and adaptability of our team in the face of unforeseen challenges.
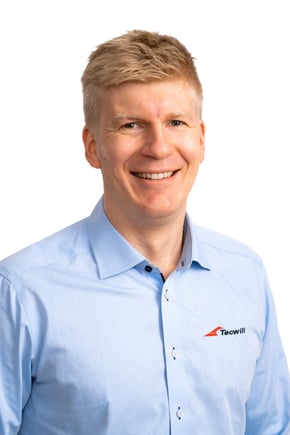