Thomas Concrete replaced the old central-mix plant with Arcamix wet-batch plant
Arcamix 4.0 wet batch plant features;
- a more accurate VSD-controlled "flying" aggregate weighing system
- a BHS twin-shaft mixer with a (5.2 yd3) 4.0 m3 batch size
- an automatic reclaimer and separate water scale for recycled water
- two separate admixture scales
- aggregate bins with a total capacity of 6x90 t.
- an overdrive type receiving hopper for aggregates, and aggregate lifting conveyor with shuttle belt
- an automatic fiber dosing system
- VSD-controlled binder augers
- customer-specific colored cement silos
- a batch control room container, an admixture container, a laboratory container
- full automatic aggregate and water heating system
Picture, And old Thomas Beton cental-mix plant.
The old factory was replaced with new low carbon concrete production technology
The old Thomas Beton concrete plant, located in the heart of Västerås, in the Mälerporten area, had been supplying concrete to the County for over 70 years. As the development and new construction in Västerås city center progressed, the question arose - was the concrete plant's location still ideal? Working together with the city of Västerås, a decision was made to relocate the concrete production to a new site in the Hackstan industrial area. While there may have been a tinge of nostalgia as the demolition began, it was exciting that the staff would now have the opportunity to work at the new concrete plant and technology. Both Thomas Betong and the city of Västerås were surely pleased with this solution.
Picture, Arcamix 4.0 wet batch plant.
A high capacity production wet batch plant with an aggregate lifting system
We had the opportunity to deliver a new Arcamix 3.0 plant to Thomas Beton in the heart of Gothenburg at the beginning of 2020, supplying concrete to the massive Västlänken double-track railway project. You can read more about project in this link.
From the beginning of negotiations, it was clear that a more robust concrete plant would be needed. The capacity of the binder silos was selected to ~ 5 x 110 t and the storage volume of aggregate bins to 6 x 90 t. The mixer size was increased by 33%, allowing 10.4 yd3 (8 m3) concrete trucks to be filled in two batches, while the 5.2 yd3 (4 m3) twin-shaft mixer "roars" in the mixing container.
Aggregates are lifted from the receiving hopper to the storage bins using a 85 feet (28 m) long lifting conveyor. The volume of the receiving hopper was determined to be approximately 30 t, leading to a decision during the design phase to lower the concrete structure of the receiving hopper below ground level. This design choice means that the ramp structure for trucks on either side of the receiving hopper does not need to be as massive.
Picture, Compact plant set-up with all necessary equipment.
Automatic fiber dispensing system
The usage of fiber (steel fibers, synthetic fibers and polypropylene fibers) in ready-mix concrete, especially the automatic dispensing of fiber into the concrete or aggregate mix, has seen a significant rise in recent years. To mix high-quality shotcrete (spray concrete), the dosing and weighing of materials, temperature and concrete mix slump must be precisely controlled.
In Västerås, fibers are dispensed with Tecwill’s innovative on-conveyor fiber feed that reduces mixing time and avoids fiber clumps. The fiber is weighed and automatically added into the aggregate while its moving on the belt. This ensures that the production capacity of the concrete plant for fiber-reinforced concrete remains consistently high from one batch to the next. The quality of fiber-reinforced concrete is uniform, and this method prevents any fiber clumps in the concrete mix.
Powerful twin shat mixer with an automatic high pressure wash-out system
For Tecwill and Thomas Concrete, it is important that the mixer fulfills the following requirements: cost and energy efficiency, reliability, short mixing times combined with a very good homogeneity, and: the mixer must match with the truck mixer size (two batches per truck). Especially when the customer needs a central-mix plant, the actual size of the mixer plays a crucial role.
The external dimensions of the mixers are relatively small compared to a large batch size. Another plus is the low mixing time – even when processing special mixtures with fibers or special admixtures.
Mixer is equipped automatically with an automatic high pressure wash-out system. Mixer can be washed during the day when having breaks, and in the end of the day when production ends. Easy maintenance is important for the operators and also in terms of maintenance costs.
Picture, Powerful twin shat mixer with an automatic high pressure wash-out system.
Goals - low carbon concrete production and meeting environmental standards
Responding to demand for new mix designs, environmental regulation aiming reducing carbon emissions and lower production costs are important requirements for all concrete plants and also for Tecwill as a batch plant manufacturer.
There are new environmentally friendly low carbon raw materials on market, for example low-carbon cement and supplementary cementitious materials (SCMs) like fly ash and slag.
However, the new materials sets new requirements for the mixing process and weighing and dosing accuracy. Wet batch technology ensures better mixing. Moreover, Tecwill's more accurate flying weighing also means reduced material use. This further contributes to resource efficiency and overall plant sustainability.
Steps you can take
More and more companies are taking action to meet today’s concrete production challenges. Many are implementing the newest wet batch production methods and introducing new low carbon materials into their operations. To remain competitive, a plant must embrace change.
Tecwill understands the diverse needs of modern concrete plants and offers a comprehensive range of future-proof solutions. From cutting-edge mixing technology to industry-leading material weighing and moisture control, Tecwill equips plants with the tools needed to keep up with the times.
Ask us more!
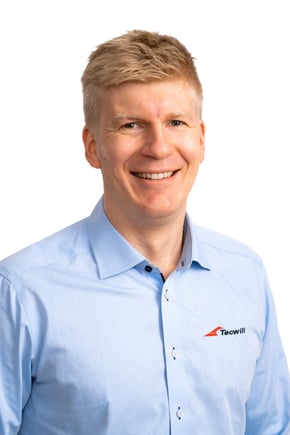