From environmental pressures to rising energy costs, concrete plants are facing a wave of new challenges. Let’s explore what has been making concrete production trickier recently – and some available solutions.
Several drivers are affecting concrete plants worldwide, requiring significant adaptation and even transformation. These include tightening regulations on dust, noise and carbon emissions, as well as the demand for new mix designs in concrete composition.
While change is a challenge, solutions already exist to keep a plant competitive. Let’s take a look at the challenges facing concrete producers and potential solutions, one by one.
1. Meeting environmental standards
Environmental regulations aimed at reducing carbon emissions are placing ever-tightening constraints on the construction and concrete industry. As governments worldwide ramp up efforts to combat climate change, concrete plants are under increasing pressure to adopt more sustainable practices.
Concrete batch plants can start by switching to new, more environmentally friendly raw materials. For example, low-carbon cement and supplementary cementitious materials (SCMs) like fly ash and slag can help cut CO2 emissions considerably.
Picture: Wet batch ready mix plant in Utah, USA.
However, the introduction of new materials sets new requirements for the mixing process and calls for higher weighting and dosing accuracy. For this, the adoption of wet batch technology is particularly effective. It ensures more accurate weighing and better mixing. Moreover, precise weighing also means reduced material use. This further contributes to resource efficiency and overall plant sustainability.
In addition, with stricter requirements for dust and noise, it gets ever more challenging to set up new dry batch plants. For example, in Texas, residents are pressuring the Texas Commission on Environmental Quality to reduce pollution from concrete production. Local neighborhoods are claiming, “It’s as if there’s a constant cloud of dust.” In turn, modern enclosed wet batch plants reduce dust and noise generation. Therefore, obtaining permits and approval from residents for these plants is easier.
2. Responding to demand for new mix designs
Fueled not just by sustainability but also by the quest for more effective building materials, concrete compositions are evolving continuously. Currently, there is a growing demand for high-strength concrete, low-carbon mix designs and other special mix designs.
As mentioned earlier, for concrete plants, this shift means incorporating new cement blends into their processes. Then follows recalibrating conventional processes with a greater focus on mixing.
In dry batch plants, concrete mixing takes place in drums. Typically, this doesn’t provide a sufficiently good mixing result. Alternatively, the time spent making needed rotations increases dramatically, reducing production capacity. The time spend at the yard making rotations is away from the time suppling concrete to the customer. Any new low-carbon materials or activators (admixtures) that bring out their properties require a flawless mixing result. Again, the easiest solution is using wet batch technology.
Picture: Drive through is the most efficient way to operate a concrete plant.
3. Increasing storage capacity
The growing complexity of concrete compositions, coupled with the need for greater material diversity, has led to an increased demand for storage capacity at concrete plants. The more materials used in production, the more storage bins and silos are needed.
What’s more, five, six or even seven aggregate bins might be needed. In areas where sand is scarce or fails to meet quality standards, it’s often made by crushing. And as there can be several fine aggregate fractions in use, separate bins are needed for all of them.
In response to this challenge, plants must expand their storage facilities and optimize their material handling processes to ensure smooth operations.
Picture: Easy loading of aggregate bins using front loader.
4. Ensuring accurate dosage and consistent mixing
Inaccurate component weighing and improper concrete mixing lead to inconsistencies in concrete properties, slump variations and even compromised structural integrity. With the introduction of new low carbon binder materials, this issue has become even more obvious.
While more beneficial for the environment, some new low-carbon cements have longer setting times, because they contain less cement and more ash and slag. This necessitates the use of activators (admixtures) to speed up the setting process. Admixtures, in turn, may introduce additional complexities to the production process. When any additives are used, the accuracy of material proportions in each concrete batch is a must. Plus, the introduction of new admixtures entails the installation of more admixture pumps.
Conventional dry batch plants often struggle with larger slump variation and cannot reach the needed quality standards. Sometimes, this variation can even be worsened by truck mixer drivers adding excessive water to the load. Therefore, investing in technologies that provide control over the mixing and weighing process should be considered.
Wet batch plants allow for more accurate weighing and better mixing, resulting in reduced variations in concrete slump – and improved overall quality. With this technology, slump is determined at the plant – with no driver intervention required. Additionally, implementing a high-end aggregate moisture control system further enhances the quality of production.
Picture: Slump control at the concrete mixing plant.
5. Addressing rising energy costs
The surge in fuel and electricity prices has significantly impacted production costs for concrete plants. Energy consumption is a major expense in concrete production. Therefore, plants are under constant pressure to find ways to reduce energy use to remain competitive in the market.
To address these concrete plant challenges, owners should consider replacing their old production plants with new, more efficient models that use less energy and fuel. Alternatively, retrofitting outdated heating systems with the newest-generation on-demand, non-boiler systems can help optimize energy use and reduce costs.
6. Enhancing workplace safety
Industry safety standards also continue to evolve. This requires concrete plants to implement more robust safety protocols to reduce the risk of accidents and injuries at the plant.
Furthermore, plants may be forced to invest in structural upgrades, such as replacing old stairs and ladders to keep up to date with the latest OSHA standards.
Sometimes, the most rational approach is to completely upgrade an outdated production plant to avoid risks.
Picture: Safe stairs and service walkways facilitate daily maintenance.
Steps you can take
More and more companies are taking action to meet today’s biggest concrete production challenges. Many are implementing the newest wet batch production methods and introducing new low carbon materials into their operations. Still, many lag behind, retaining their outdated dry batch plants.
To remain competitive, a plant must embrace change.
Tecwill understands the diverse needs of modern concrete plants and offers a comprehensive range of future-proof solutions. From cutting-edge mixing technology to industry-leading material weighing and moisture control, Tecwill equips plants with the tools needed to keep up with the times.
Our wet batch plants are a perfect match for the evolving concrete production landscape.
Ask us more!
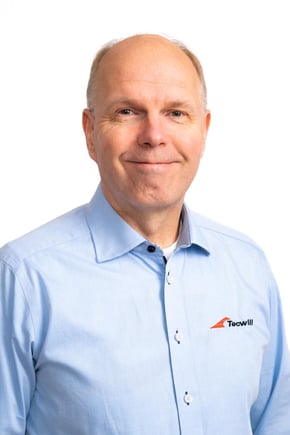