Concrete – or mortar?
One of the biggest limitations to 3D concrete printing today is that the printing material is actually mortar rather than concrete. Mortar, which consists of sand, cement, admixture and water, is easier for a 3D printer to handle, pump and print than concrete.
Mortar, however, is brittle and lacks sufficient tensile strength because it does not contain any larger-sized aggregate. Although mortar has very high cement content and the material then becomes prohibitively expensive.
Mortar has additional limitations, as well. House height is limited to one or two floors because of the poor stability of mortar. The risk of cracking increases, and its large cement content causes high carbon dioxide emissions. Plus, the mortar mix requires more admixtures to improve the quality of the printed outcome.
Even if a batch plant would like to print with concrete, the conventional batch plant and process cannot reach the dosing accuracy and precision needed for top-quality results. Concrete tends to cause printer breaks. Additionally, the end quality is unlikely to fulfill the current requirements of the construction industry.
Revolutionizing the process
Tecwill began innovating a new solution for 3D concrete printing some years ago. The company is now launching a brand-new, super mobile, compact 3D-Mix plant. The plant is specifically designed to use concrete printers for top-quality results at radically slashed production costs.
Tecwill’s concept allows 3D printing companies to use aggregate sizes of up to ½” (12 mm). The coarse aggregate reduces the cement content in the concrete, improves its volumetric stability and increases printing efficiency. This results in a cheaper, sturdier mix and lower ready construction costs.
The 3D-Mix plant produces concrete suitable even for multi-floor houses, thanks to its improved strength and stability.
Based on proven technology
Unlike conventional 3D printing processes, Tecwill’s unique 3D-Mix concept is based on proven technology used in all Tecwill’s other plants. The technology is not new – it is just packaged in a new, more compact form for a highly mobile solution into single unit.
This technology includes the “flying” weighing system with Tecwill’s OptiMoist moisture control. It also features in-built artificial intelligence (AI) to minimize cement use, produce less off-spec concrete and reduce printer breaks.
Tecwill’s technology ensures outstanding concrete accuracy with low variations for the best possible production. This helps producers easily fulfill the ever-stricter construction requirements for 3D concrete printing.
Lowers the carbon footprint
To help the concrete industry better contribute to climate change and become more sustainable, Tecwill has developed many pioneering technologies. The 3D-Mix concrete plant focuses on lowering CO2 emissions in 5 specific ways:
• More accurate weighing
• Better moisture management
• Improved temperature control
• Smoother plant logistics
• Use of concrete instead of mortar
Moreover, the new concrete plant minimizes dust and noise, making it ideal for urban areas.
All-in-one plant
Everything needed for Tecwill’s 3D printing concrete plant fits neatly into just one extremely compact 40 ft (12 m) container sized module. As a result, the 3D-Mix concrete plant has a low profile and small footprint.
This self-erecting, highly mobile plant – together with the concrete printer – can be easily moved from one house to the next. The hydraulic legs simply lift the container into position at the new construction site, and the plant is ready to go.
The same plant can be used for all mixes needed for a single house – from the foundation, walls and other structures to the floors, sidewalks and roads.
Disruptive opportunities
The 3D-Mix concrete plant offers many opportunities for businesses involved in 3D printing to gain traction in lucrative house construction projects.
3D printing enables the production of customized and complex designs. It saves costs and time by reducing labor requirements, material waste and transportation needs. Construction companies now have the opportunity to serve the growing industry with safe, affordable and sustainable practices.
With Tecwill’s innovations, 3D concrete printing businesses can take a giant leap forward with better concrete quality and lower production costs. Additionally, they support sustainable construction practices with lower waste, carbon emissions and energy consumption.
Tecwill’s 3D-Mix concrete plant sets businesses up to stay ahead of the competition. It also helps them meet the ever-stricter building regulations for high-quality, affordable 3D-printed homes and carbon reduction.
Interested?
Read more about 3d printing on our solution page.
Contact me to find out more.
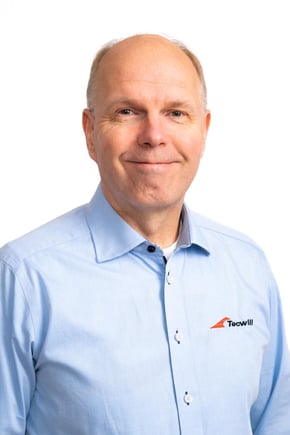