The scope of supply consisted of two WillControl control systems (production line 1 and production line 2), two computers and displays, two new logics, two sets of weighing amplifiers and equipment for the modernization of the automation cabinets.
Tecwill delivered the WillControls and the additional equipment for Lujabetoni Oy's precast concrete plant to Hämeenlinna in January 2018. The existing logics, weighing amplifiers and all programs as well as the input and output cards were replaced.
Short installation time thanks to intense pre-testing
The installation and start-up of all control equipment and programs were carried out within just four days during the first week of January 2018. This was possible because the system and programs were simulated and tested beforehand at the Tecwill factory before starting the installation in Hämeenlinna.
Modern weighing amplifiers enable rapid start-up
The weighing amplifiers were selected on the basis that scales´ calibration values of the existing logic could be utilized directly in the new amplifiers. This significantly speeded up the start-up of the production lines, since there was no need to pre-calibrate the new scales separately, the taring controls were sufficient. The new weighing amplifiers are fully digital, which, in addition to the above-mentioned benefits, makes it easy to replace devices. If a device needs to be replaced no calibration by using weights or a hydraulic press is required.
The pre-installation and the comprehensive pre-testing of the programs made it possible that the production started already two days after completion of the installation – concrete was already made on the first day of the second week! The timetable was really ambitious, because of the factory’s two separate production lines, both having their own control systems with standard equipment.
Possible failure will not stop the entire factory
The project had its challenges.
On the first production line the concrete is transported to the element factory by a bucket conveyor system, the second line is equipped with an aggregate lifting system. Both lines have 4-5 scales and their own control logics however have to communicate with each other as far as the use of the material of the shared aggregate bins is concerned.
There are two logics – meaning that if one line stops or something causes a failure, it won’t stop the production of the whole factory.
The new systems also had to transfer all material and recipe data from a separate program, which required its own transfer program.
Proper preparation prevents production losses
Proper preparation prevents from interruption of the production process, a high risk when renewing an existing system. Normally the functioning production process is stopped and restarted once the new system has been replaced.
In most the cases the production process will not have been tested in advance, which is why the testing of the programs has to be carried out on site. With the consequence that it is not possible to reliably estimate in advance how long the replacement process will take – one day, a few days or a couple of weeks?
The good news is that the WillControl system and all processes can be fully tested beforehand at the Tecwill factory, which means that during the start-up phase the personnel can concentrate on the actual installation of the equipment and the training of the customer.
The process virtualization used for the testing has been developed by Tecwill Oy.
Tecwill did provide what Lujabetoni Oy wanted: Systems for a safe and stable production of high-quality precast and ready-mixed concrete and the ability to easily extend the service and maintenance system as well as the control and electrical system in the future.
Accurate weighing and precision save cement and reduce customer complaints
The WillControl control system can use the mathematical model built for each dosing device and by this a higher precision of the dosing can be achieved without losing production capacity. Improving the precision of the dosing reduces the variation in concrete strength, which reduces the need for adding extra cement in a concrete mix. A low standard deviation in the concrete production process will also reduce the number of complaints of end customers. At the same time costs for repairs of prefabricated concrete elements with defects, withdrawels of RMC due to lack of quality and necessary after-sales services can minimized. Thus, the WillControl control system improves the profitability.
To keep the service and maintenance costs low, it is recommended to minimize the number of old control devices because they cause interferences. All parts of the control and electrical system that will not be renewed in the modernization process may later cause damage. They can cause production downtimes and result in fault analysis costs and repair costs due to missing or incomplete drawings and lack of spare parts. It is also important to consider that old equipment in the electrical cabinet may contain a high risk of fire. By replacing the control and electrical equipment it is easier to get spare parts in the future and the fire risk gets minimized.
Lujabetoni´s plant in Hämeenlinna
Lujabetoni´s plant in Hämeenlinna produces ready-mix and concrete for prefabricated elements (columns, beams, pre-stressed concrete slabs, hollow-core and thin-shell slabs, balcony and platform slabs, walls, Luja flue elements) – completey according to customers’ requirements.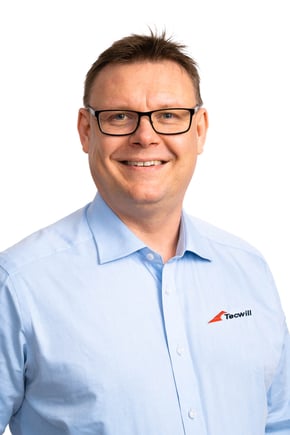