Concrete mixing plants are not immune to cold temperatures. Especially in regions prone to longer winter months, insulated facilities are crucial for efficient concrete production. Still, winter insulation should be an integral part of any concrete mixing plant. But how do you make sure you’re properly prepared?
Most often, the need for ready-mix concrete production peaks in spring, summer and autumn. In turn, mobile batch plant relocations usually take place during the winter.
If your production continues throughout the winter, it is important to ensure smooth operations and product delivery. That’s when proper insulation for concrete batching plants plays an important role.
A concrete mixing plant should be designed to reliably and cost efficiently produce ready-mix concrete even in the coldest winter months when air temperatures fall significantly below freezing. If concrete temperatures drop below +68 °F (+20 °C), the chemical reactions that strengthen the concrete slow down, leading to weaker concrete.
Therefore, it is essential to deliver temperature controlled concrete even during the winter. To ensure this, all production areas that handle additives, water or cold aggregate should be heated. Additionally, all structures, pipelines and hoses should be well insulated to avoid any heat loss.
Carefully designed and installed winter insulation (enclosure) ensures uninterrupted production all year round. It also improves the production environment and brings significant savings in heating costs. Since the concrete temperatures are always kept at the desired level, quality control is easier.
With poor winter equipment or subpar insulation, concrete production cannot be smooth and efficient. Energy consumption increases. The plant’s capacity decreases since the aggregate and water cannot be heated quickly enough. Dosing becomes more difficult if the aggregate in the silos is not molten. Even the waiting time of concrete trucks is affected.
Getting ready for winter before startup
It takes time to install adequate winter insulation in cold and humid conditions. But having proper insulation in place is non-negotiable. No ready-mix concrete supplier should ever have to worry whether the night was too cold or not. Winter should not be a cause for additional concerns.
Ideally, mobile, module-based concrete mixing plants should be equipped and pre-installed already at the production factory. Winter insulation should be an integral part of every plant structure. Having winter equipment preinstalled at the factory eliminates the need for dismantling when the concrete batching plant is moved to a new site.
This saves commissioning time at the next plant location, allowing production to be started up faster. Plus, it significantly reduces relocation costs.
Reinstallation of winter equipment when moving
Time schedules are often challenging with construction projects. It is commonly the case that ready-mixed concrete delivery dates are set and time schedules are binding. Therefore, it is important to get production back up and running promptly.
Once a mobile concrete mixing plant has finished operations at one site and is ready to be relocated, the transfer process needs to be as smooth and efficient as possible. This is no place for unexpected surprises or unforeseen and time-consuming work phases.
Winter insulation checklist
Here is a checklist to help you make sure the insulation of your concrete mixing plant has all the proper requirements to be prepared for below-zero operating conditions.
-
Check if the cold spots have been minimized between the steel structure and the outdoor air. Both sides of the steel structure must have insulation, so the surfaces do not come in contact with either the outside or inside air of the mixing plant. This minimizes and even eliminates cold spots
-
Check if the insulation has been installed in warm conditions in the production hall or on site
-
Check if the winter equipment is part of the base construction or if you have to disassemble and transport it separately
-
Check the insulation panel thickness and material used. 3" (70–80 mm) PIR insulation panels are the most optimal for concrete mixing plants. For instance, 3" (80 mm) PIR panels have a thermal conductivity of 0.027 W/mK
-
Check the power of the heating system and how it affects the energy bills
-
Check if the water equipment is also thermally insulated, if there is any easy connection point – or need for a plumber
-
Check the insulation of admixture hoses between the tanks and the scale
-
Check if the final cost includes the proper winter equipment for batching plants
If you can check off most of this list, you can be assured you are prepared for efficient concrete production in winter.
After all, carefully designed insulation and other appropriate winter equipment ensure uninterrupted concrete production all year round – regardless of the cold air and the weather outside.
Read more about mobile concrete mixing plants »
If you have any further questions, do not hesitate to contact Teemu Tuominen or fill out this contact form.
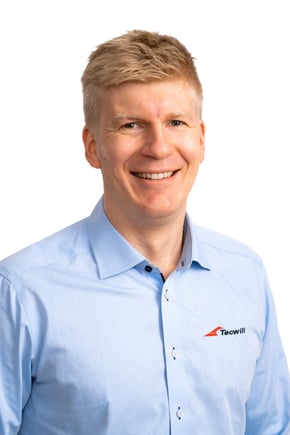