TABLE OF CONTENTS
Tecwill ready-mix concrete batch plants
We help ready-mix concrete companies around the world by manufacturing multipurpose and energy-efficient concrete batching plants. These enable our customers to produce the world’s best concrete with lower production costs and a smaller carbon footprint.
Our ready-mix concrete batching plant:- Utilizes new technology and offers significant savings in production costs
- Saves cement and reduces CO2 emissions during concrete production
- Increases production capacity and avoids production breaks
Modules of a Tecwill concrete mixing plant
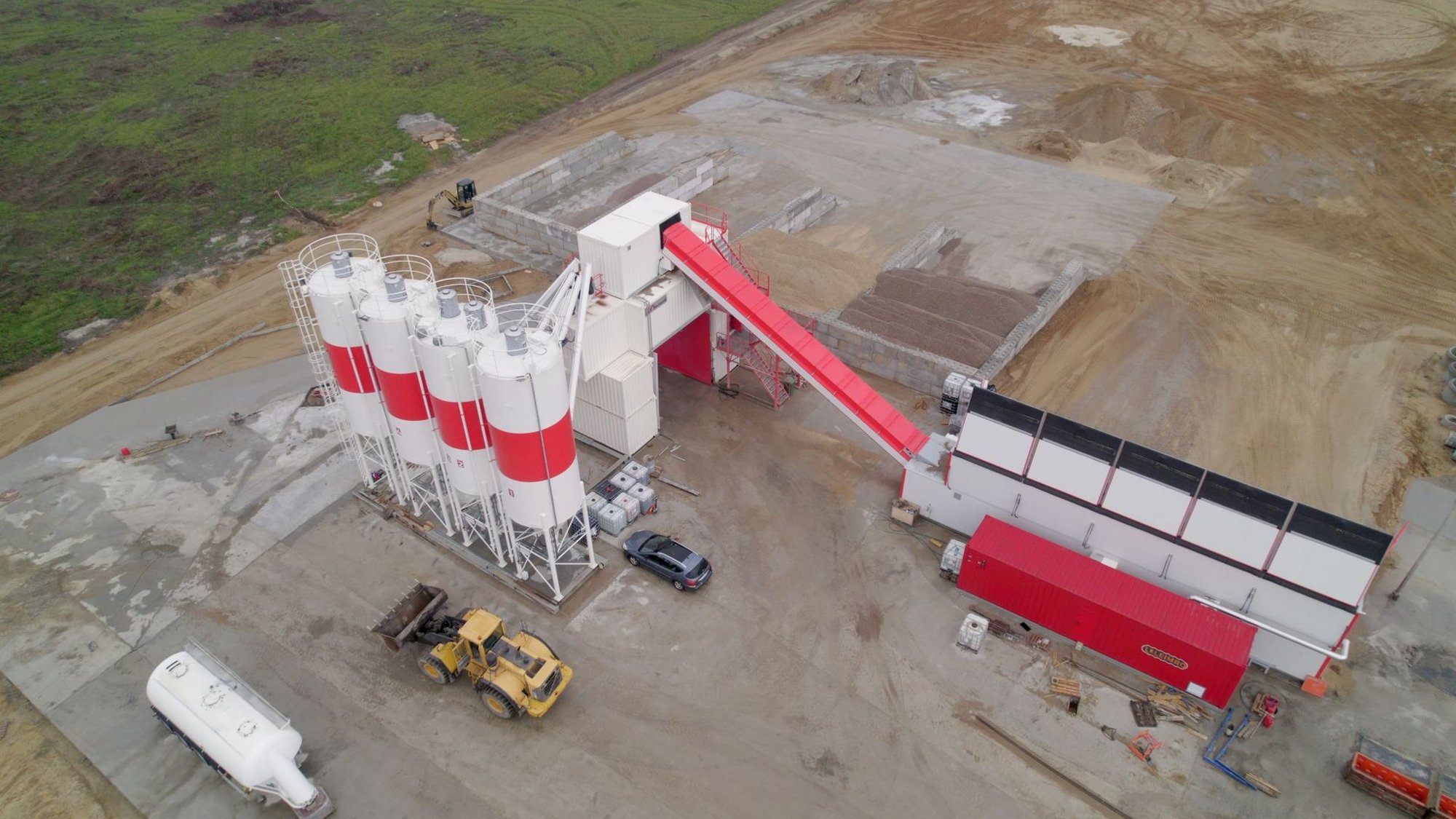
Multifunctional hybrid concrete batch plant
- Ready-mix concrete
- Shotcrete with fibers (spray concrete)
- Self-consolidating concrete
- RCC - roller compacted concrete
- Paving concrete
- Lean concrete
- Zero slump concrete
- Colored concrete using powder, C pigment or granule pigments
Our improved weighing technology can take care of dosing and mixing of new supplementary cementitious materials and “activators” like;
- Fly ash
- Slag
- Polymer cement
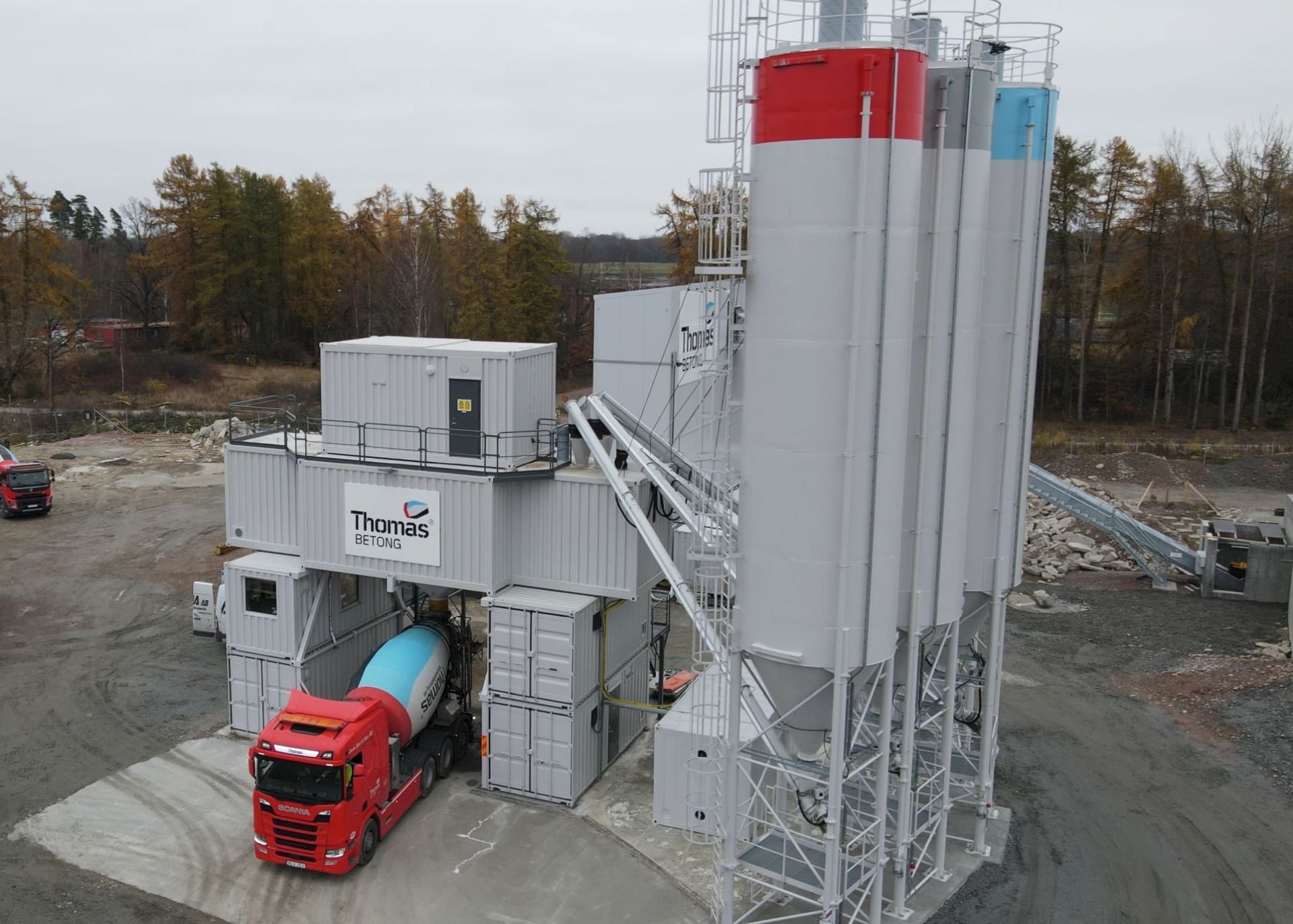
Why choose Tecwill – how are we different?
Tecwill’s high-precision “flying” weighing system saves up to 30 kg/m3 in cement and reduces CO2 emissions in concrete production.
Our “flying” aggregate weighing system eliminates the need to add extra cement to the mix design to compensate for inaccurate weighing and dosing.
- More accurate weighing
- Less cement
- Correct slump
Tecwill’s OptiMoist system allows moisture content of all aggregate fractions to be measured by one common moisture probe.
The right amount of water in the concrete batch shortens the mixing time and reduces quality issues.
- Improved aggregate moisture control
- Correct slump
- Lower probe costs
- Easy calibration
Tecwill’s modular construction makes the concrete plant fast to install, even in winter, and easy to relocate and reinstall year-round.
Tecwill preassembles the complete concrete plant at its own factory. This includes pre-wiring, piping, thermal insulation enclosure and plant testing.
- Fast set-up time, even in winter
- Easy to relocate and reinstall year-round
- Reliable winter operations
Frequently asked questions
These are questions we’re often asked. We hope you find these helpful. If you still have a question we haven’t addressed, please contact us directly.
The production of cement as a raw material for concrete is a major source of carbon dioxide emissions. Tecwill’s technology has been specifically developed to reduce the amount of cement used in concrete, thereby reducing CO2 emissions.
Our solution improves the energy efficiency of concrete plants and increases water recycling to cut back on CO2 emissions.
When manufacturing our products, we reduce our own environmental impact by using recycled steel and developing new ways to minimize our material consumption.
We have developed a completely new “flying” aggregate weighing system that ensures accurate dosing of raw materials and improved aggregate moisture measuring.
Our new technology with modular construction makes it possible to manufacture the entire concrete plant at the factory, where it can be fully tested before delivery. Quick on-site installation and production startup are ensured with our factory-installed electricity, piping and thermal insulation.
Our concrete plants are hybrid plants. The same solution is suitable for:
- Central mix plant
- Transit mix plant
- Portable concrete plant
- Mobile concrete batch plant
- Shotcrete plant
- Paving plant
You can produce all types of concrete mix designs, including:
- Ready-mix concrete
- Shotcrete
- Roller-compacted concrete
- Zero-slump concrete
- Self-consolidating concrete
- Precast concrete
It is often thought that tires on a concrete batch plant make it portable. A plant with tires needs just as many crane hours and similar foundations as a concrete batch plant without tires.
Tires and axles cause cramped and unsafe maintenance spaces. They complicate the weighing and dosing process.
A concrete plant with tires is also hard to use in winter conditions because it still needs an enclosure and insulation – after which it is no longer portable because of the enclosure.
Tecwill mobile concrete plants are based on a patented installation mechanism and a flying weighing system that enable a preassembled enclosure. Tecwill mobile concrete plants have fast set-up time, even in winter, and can be reinstalled year-round.
Concrete batch plant models
The Mega Arcamix concrete batch plant is a hybrid production unit for paving, lean, road or reinforced concrete (RC) and ready-mix concrete.
Mega Arcamix is our largest and most efficient concrete mixing plant with a capacity of up to 200 m3/h (260 yd3/h).
See productThe Super Arcamix versatile hybrid concrete plant is well suited to urban environments and can be used to produce various types of concrete. Thanks to its modular construction, the plant is easy to relocate.
This multipurpose concrete production plant offers a capacity of up to 150 m3/h (200 yd3/h).
See productThe Arcamix concrete mixing plant is based on the dimensions of sea containers. This solution gives customers all the equipment and facilities they need to produce concrete with a small footprint.
The plant is suitable for the production of various types of concrete and has a capacity of up to 130 m3/h (170 yd3/h).
See productCobra C120 is the largest plant model in the Cobra family. The concept represents the latest way of approaching concrete production. The same solution can be used as a mobile on-site and as a central mix plant. The plant is quick to install and easy to move to a new location.
The plant is suitable for the production of various types of concrete and has a capacity of up to 120 m3/h (160 yd3/h).
See productCobra C80 features an exceptionally small footprint and is equipped with a countercurrent planetary mixer. The quick installation and production startup make it suitable for project sites and central mix operations.
The plant is suitable for the production of various types of concrete and has a capacity of up to 80 m3/h (105 yd3/h).
See productCobra C40 is well suited to the production of ready-mix or precast concrete. The efficient countercurrent planetary mixer works smoothly with all types of concrete. This model has a small footprint.
The plant is suitable for the production of various types of concrete and has a capacity of up to 40 m3/h (52 yd3/h).
See productTecwill in brief
- 30 years of experience designing and manufacturing concrete plants
- Our technology significantly reduces CO2 emissions from concrete production
- Global operations
- Head office, assembly factory and testing facility in Joensuu, Finland
Want more information?
Watch the Arcamix concrete plant delivery video.
Watch the videoThe Arcamix concrete batch plant mixes concrete downtown in Gothenburg, Sweden.
Read moreThe Arcamix brochure gives more information about the models, features, benefits and accessories.
Download the brochureWatch the video of Cobra concrete plant in operation
Watch the videoThe Cobra plant mixes concrete for the largest wind turbine park in the world.
Read moreThe Cobra brochure gives more information about the models, features, benefits and accessories.
Download the brochure